Lithium battery heat-conducting flame-retardant material and preparation method thereof
A technology for flame retardant materials and lithium batteries, applied in the field of thermal conductive materials, can solve the problems of dust explosion, unsatisfactory thermal conductive materials, hidden safety hazards, etc., and achieve the effects of low raw material cost, fast preparation method, scientific and reasonable proportioning and compatibility
- Summary
- Abstract
- Description
- Claims
- Application Information
AI Technical Summary
Problems solved by technology
Method used
Image
Examples
Embodiment 1
[0023] Get the following raw materials by weight: 35 parts of granite, 12 parts of magnetite, 4 parts of coal, 2.5 parts of carbon (diamond powder), 4 parts of malachite, 4 parts of zeolite, 9 parts of Montmory pumice, 17 parts of carboniferous stone , 8 parts of gypsum, 9 parts of talcum powder, and 11 parts of silver. Grind the above components into powder and mix them uniformly to obtain a mixture filler. Heat it at a constant speed to 780°C at room temperature and sinter at a constant temperature for 6 hours. After cooling down to room temperature, further grinding shredded for use;
[0024] Take 29 parts of alumina ceramics and grind them as ceramic fillers, heat them up to 780°C at a constant speed and sinter at a constant temperature for 6 hours, then cool down to room temperature and then grind them further for use;
[0025] Then the crushed ceramic filler and the mixture filler are fully mixed and evenly heated to 1180°C for sintering to obtain the filler, which is cr...
Embodiment 2
[0028] Get 30 parts of following raw materials granite by weight, 15 parts of magnetite, 3 parts of coal, 3 parts of carbon (diamond micropowder), 3 parts of malachite, 5 parts of zeolite, 8 parts of Montmory pumice, 20 parts of carbonite, 5 parts of gypsum, 10 parts of talc powder, and 10 parts of silver. Grind the above components into powder and mix them evenly to obtain a mixture filler. Heat up to 780°C at a constant rate at room temperature and sinter at a constant temperature for 6 hours. After cooling down to room temperature, further crush stand-by;
[0029] Take 28 parts of alumina ceramics and grind them as ceramic fillers, heat them up to 780°C at a constant speed and sinter at a constant temperature for 6 hours, then cool down to room temperature and then grind them further for use;
[0030] Then the crushed ceramic filler and the mixture filler are fully mixed and evenly heated to 1180°C for sintering to obtain the filler, which is crushed to 200-300 microns,
...
Embodiment 3
[0033] Get the following raw materials by weight: 40 parts of granite, 10 parts of magnetite, 5 parts of coal, 2 parts of carbon (diamond powder), 5 parts of malachite, 3 parts of zeolite, 10 parts of Montmori pumice, 15 parts of carbonite , 10 parts of gypsum, 8 parts of talcum powder, and 12 parts of silver. Grind the above components into powder and mix them evenly to obtain a mixture filler. Heating at a constant rate at room temperature to 780°C and sintering at a constant temperature for 6 hours, then cooling down to room temperature and then further grinding shredded for use;
[0034] Take 30 parts of alumina ceramics and grind them as ceramic fillers, heat them up to 780°C at a constant speed and sinter at a constant temperature for 6 hours, then cool down to room temperature and then grind them further for use;
[0035] Then the crushed ceramic filler and the mixture filler are fully mixed and evenly heated to 1180°C for sintering to obtain the filler, which is crushe...
PUM
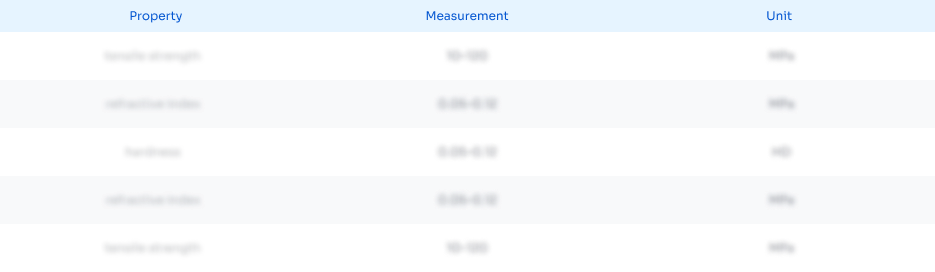
Abstract
Description
Claims
Application Information

- Generate Ideas
- Intellectual Property
- Life Sciences
- Materials
- Tech Scout
- Unparalleled Data Quality
- Higher Quality Content
- 60% Fewer Hallucinations
Browse by: Latest US Patents, China's latest patents, Technical Efficacy Thesaurus, Application Domain, Technology Topic, Popular Technical Reports.
© 2025 PatSnap. All rights reserved.Legal|Privacy policy|Modern Slavery Act Transparency Statement|Sitemap|About US| Contact US: help@patsnap.com