Method of cutting force prediction and temperature prediction for end-milling cutting
A technology of cutting force prediction and end milling cutting, which is applied in special data processing applications, instruments, electrical digital data processing, etc., and can solve the problems of lack of methods for predicting cutting force and temperature of end milling
- Summary
- Abstract
- Description
- Claims
- Application Information
AI Technical Summary
Problems solved by technology
Method used
Image
Examples
Embodiment Construction
[0181] In order to make the object, technical solution and advantages of the present invention more clear, the present invention will be further described in detail below in conjunction with the examples. It should be understood that the specific embodiments described here are only used to explain the present invention, not to limit the present invention.
[0182] The application principle of the present invention will be further described below in conjunction with the accompanying drawings and specific embodiments.
[0183] Such as figure 1 As shown, the method for predicting the cutting force for end milling according to the embodiment of the present invention includes the following steps:
[0184] S101: Analyzing the end milling cutting process, respectively establishing a milling force prediction model based on the average cutting force and a milling force prediction model based on the bevel cutting mechanism;
[0185] S102: In the process of solving the milling force co...
PUM
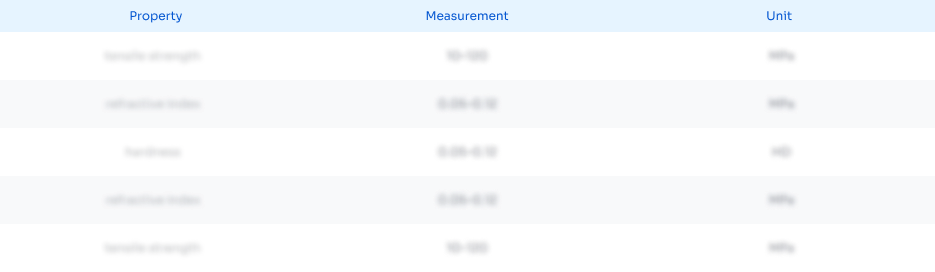
Abstract
Description
Claims
Application Information

- R&D
- Intellectual Property
- Life Sciences
- Materials
- Tech Scout
- Unparalleled Data Quality
- Higher Quality Content
- 60% Fewer Hallucinations
Browse by: Latest US Patents, China's latest patents, Technical Efficacy Thesaurus, Application Domain, Technology Topic, Popular Technical Reports.
© 2025 PatSnap. All rights reserved.Legal|Privacy policy|Modern Slavery Act Transparency Statement|Sitemap|About US| Contact US: help@patsnap.com