Separating system and separating method for residual monomers in polymer viscous liquid
A viscous liquid and residual monomer technology, applied in separation methods, chemical instruments and methods, evaporator accessories, etc., can solve the problems of high technical difficulty and high equipment cost, and achieve the effect of simple process, high thermal effect and cost reduction
- Summary
- Abstract
- Description
- Claims
- Application Information
AI Technical Summary
Problems solved by technology
Method used
Image
Examples
Embodiment 1
[0055] 1) Preparation of test samples
[0056] In the reactor, 100 kg of crude modified HDI biuret that had been prepolymerized was sampled, and the residual HDI monomer content was detected to be 12.4 wt%.
[0057] 2) Use the separation device of the present invention to remove the residual HDI monomer in the modified HDI biuret
[0058] a. Use a vacuum pump to evacuate the system, and the vacuum degree is 0.070-0.085Mpa; after the air is purified by the dryer, it enters the gas heater and is heated to 130°C.
[0059] b. Maintain the normal operation of the agitator in the reaction kettle, pass the heated air into the gas dispersion pipe at the bottom of the reaction kettle, and enter the kettle through multiple small holes on the gas dispersion pipe, so that the HDI biuret viscous liquid bubbles and evaporates Out of residual HDI monomer.
[0060] c. The gas with residual HDI monomer is pumped to the top of the reactor under vacuum suction, enters the condenser connected t...
Embodiment 2
[0063] 1) Preparation of test samples
[0064] In the reactor, 100kg of crude HDI trimer that had been prepolymerized was sampled, and the residual HDI monomer content was detected to be 19.3wt%.
[0065] 2) Use the separation device of the present invention to remove the residual HDI monomer in the HDI trimer
[0066] a. Use a vacuum pump to evacuate the system, and the vacuum degree is 0.070-0.085Mpa; after the air is purified by the dryer, it enters the gas heater and is heated to 120°C.
[0067] b. Maintain the normal operation of the agitator in the reaction kettle, pass the heated air into the gas dispersion pipe at the bottom of the reaction kettle, enter the kettle through multiple small holes on the gas dispersion pipe, and make the HDI trimer viscous liquid bubble, Residual HDI monomer was evaporated.
[0068] c. The gas with residual HDI monomer is pumped to the top of the reactor under vacuum suction, enters the condenser connected to the reactor, separates the H...
Embodiment 3
[0071] 1) Preparation of test samples
[0072] In the reactor, 100 kg of the crude product of the prepolymerized TDI prepolymer was sampled, and the residual TDI monomer content was detected to be 8.3 wt%.
[0073] 2) Use the separation device of the present invention to remove residual TDI monomer in the TDI prepolymer
[0074] a. Use a vacuum pump to evacuate the system, and the vacuum degree is 0.070-0.085Mpa; after the air is purified by the dryer, it enters the gas heater and is heated to 120°C.
[0075] b. Maintain the normal operation of the agitator in the reaction kettle, pass the heated air into the gas dispersion pipe at the bottom of the reaction kettle, enter the kettle through multiple small holes on the gas dispersion pipe, and make the TDI prepolymer viscous liquid bubble, Residual TDI monomer was evaporated.
[0076] c. The gas with residual TDI monomer is pumped to the top of the reactor under vacuum suction, enters the condenser connected to the reactor, s...
PUM
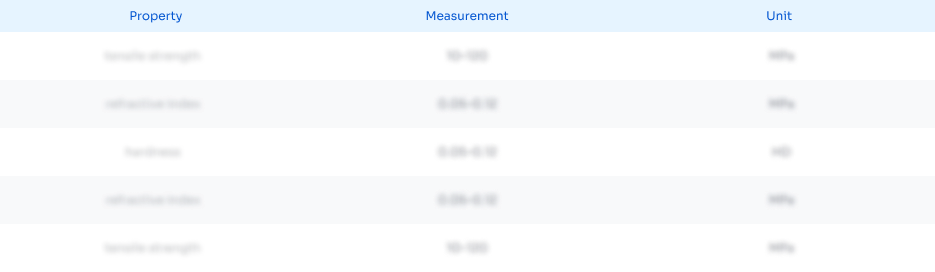
Abstract
Description
Claims
Application Information

- R&D
- Intellectual Property
- Life Sciences
- Materials
- Tech Scout
- Unparalleled Data Quality
- Higher Quality Content
- 60% Fewer Hallucinations
Browse by: Latest US Patents, China's latest patents, Technical Efficacy Thesaurus, Application Domain, Technology Topic, Popular Technical Reports.
© 2025 PatSnap. All rights reserved.Legal|Privacy policy|Modern Slavery Act Transparency Statement|Sitemap|About US| Contact US: help@patsnap.com