Method for evaluating sensitivity of edge crack of high-strength thin steel plate
A technology for edge cracks, evaluation methods, applied in directions such as testing material strength using applied stable tension/compression
- Summary
- Abstract
- Description
- Claims
- Application Information
AI Technical Summary
Problems solved by technology
Method used
Image
Examples
Embodiment 1
[0027] When using the evaluation method for edge crack sensitivity of high-strength thin steel plate of the present invention, a certain HC420 / 780DPD+Z dual-phase steel is selected as an example, and the edge crack sensitivity is evaluated by the method of the present invention.
[0028] The thickness of the steel plate is selected to be 1.2mm. Firstly, wire cutting is used and the edge is milled with a milling cutter. The edge is polished with No. 800 sandpaper to obtain a standard sample, and the steel ball mold is bulged on a plate forming test machine. A non-contact three-dimensional strain analyzer is used to track the strain of the sample during the bulging process. Such as image 3 As shown, the necking strain state indicated by point A is obtained. see image 3 , the forming limit curve of the steel grade and the strain state (point B) at the rupture point of the single tensile specimen are given as a reference, which is not necessary in this test.
[0029] Five sam...
Embodiment 2
[0031] Select HC340LA low-alloy high-strength steel with a thickness of 1.6mm, first use wire cutting and mill the edge with a milling cutter, and polish the edge with No. 800 sandpaper to obtain a standard sample, and perform steel ball mold bulging on a plate forming test machine. Use a non-contact three-dimensional strain analyzer to obtain the principal strain of the standard sample when it necks and the principal strain when it ruptures (reference, not necessary). Then, five samples with different edge states were prepared by trimming die, and the steel ball die bulging was carried out on the plate forming test machine. A non-contact three-dimensional strain analyzer was used to obtain the principal strain at the point where the sample just broke. see Figure 5 , gives the comparison of the principal strains of rupture obtained by the specimens in different edge states and the principal strains of the standard specimens during necking and rupture. Necking principal stra...
PUM
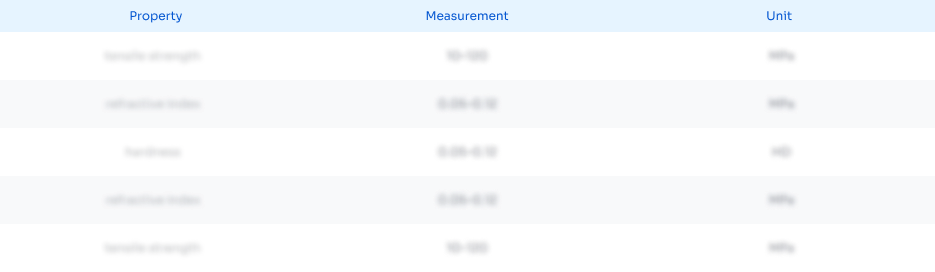
Abstract
Description
Claims
Application Information

- R&D Engineer
- R&D Manager
- IP Professional
- Industry Leading Data Capabilities
- Powerful AI technology
- Patent DNA Extraction
Browse by: Latest US Patents, China's latest patents, Technical Efficacy Thesaurus, Application Domain, Technology Topic, Popular Technical Reports.
© 2024 PatSnap. All rights reserved.Legal|Privacy policy|Modern Slavery Act Transparency Statement|Sitemap|About US| Contact US: help@patsnap.com