Method for preparing polymer composite material by expanded perlite
A composite material and an intumescent technology, which is applied in the field of intumescent perlite micropowder and the preparation of polymer composite materials, can solve problems such as difficulty in dispersing inorganic fillers, and achieve low price, improved thermal decomposition temperature and flame retardant performance, and good ore quality. Effect
- Summary
- Abstract
- Description
- Claims
- Application Information
AI Technical Summary
Problems solved by technology
Method used
Image
Examples
Embodiment 1
[0019] (1) Sieve and grind the expanded perlite. Dry in an oven at 80°C for 5 hours.
[0020] (2) Weigh 5g of expanded perlite micropowder and 95g of polypropylene resin, and carry out melt blending with a twin-screw extruder after uniform mixing.
[0021] (3) Processing the mixture obtained in the step (2) through an injection molding machine, and injection molding to obtain a polypropylene expanded perlite composite material product.
[0022] The obtained composite material is observed by transmission electron microscope and scanning electron microscope, and it is found that the expanded perlite micropowder is evenly dispersed in the polypropylene matrix, indicating that the expanded perlite / polymer composite material has been prepared.
[0023] Table 1 Effect of expanded perlite on flame retardant properties of polypropylene
[0024]
[0025] It can be seen from Table 1 that the oxygen index of the expanded perlite / polypropylene (20 / 80) sample is 8.9% higher than that ...
Embodiment 2
[0027] (1) Sieve and grind the expanded perlite. Dry in an oven at 60°C for 4 hours.
[0028] (2) Weigh 60g of expanded perlite micropowder and 60g of ethylene-vinyl acetate copolymer, knead with a double-roller mill, add 2g of calcium stearate, and mix at about 80°C to obtain expanded perlite / ethylene-vinyl acetate Copolymer composites.
[0029] The obtained composite material is observed by transmission electron microscope and scanning electron microscope, and it is found that the expanded perlite micropowder has been uniformly dispersed in the ethylene-vinyl acetate copolymer matrix, indicating that the expanded perlite / ethylene-vinyl acetate copolymer composite material has been prepared.
[0030] Table 2 has listed the impact of expanded perlite on the flame retardancy of ethylene-vinyl acetate copolymer, as can be seen from the table: the oxygen index of expanded perlite / ethylene-vinyl acetate copolymer (60 / 60) is compared Because the pure ethylene-vinyl acetate copoly...
Embodiment 3
[0035] (1) Sieve and grind the expanded perlite. Dry in an oven at 60°C for 6 hours.
[0036] (2) Take by weighing 45g expanded perlite micropowder, 55g polylactic acid resin, carry out melt blending with twin-screw extruder after uniform mixing.
[0037] (3) Processing the mixture obtained in the step (2) through an injection molding machine, and injection molding to obtain a polylactic acid expanded perlite composite material product.
[0038] The obtained composite material was observed by transmission electron microscope and scanning electron microscope, and it was found that the expanded perlite micropowder was uniformly dispersed in the polylactic acid matrix, indicating that the expanded perlite / polymer composite material had been prepared.
PUM
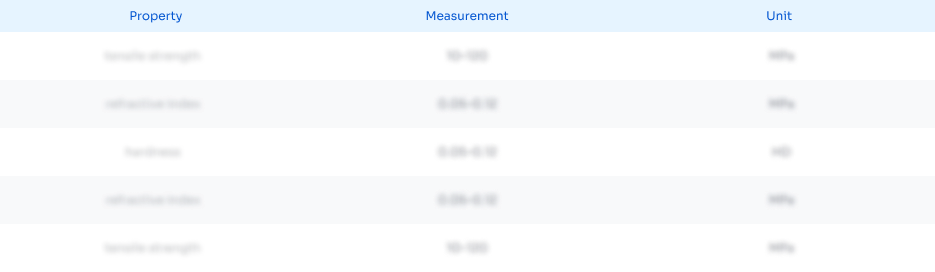
Abstract
Description
Claims
Application Information

- Generate Ideas
- Intellectual Property
- Life Sciences
- Materials
- Tech Scout
- Unparalleled Data Quality
- Higher Quality Content
- 60% Fewer Hallucinations
Browse by: Latest US Patents, China's latest patents, Technical Efficacy Thesaurus, Application Domain, Technology Topic, Popular Technical Reports.
© 2025 PatSnap. All rights reserved.Legal|Privacy policy|Modern Slavery Act Transparency Statement|Sitemap|About US| Contact US: help@patsnap.com