A kind of autoclaved aerated block and its preparation method
An autoclaved aeration and block technology is applied in the field of silicate building materials, which can solve the problems of increased cement production cost, high transportation cost and high water content, and achieves the effects of low cost, simple process and reduced leaching content.
- Summary
- Abstract
- Description
- Claims
- Application Information
AI Technical Summary
Problems solved by technology
Method used
Image
Examples
preparation example Construction
[0030] The present invention also provides a method for preparing the autoclaved aerated block of the present invention, the method comprising the steps of:
[0031] S1. Mixing siliceous raw materials with polluted acid slag to obtain siliceous slurry;
[0032] S2, mixing the siliceous slurry in step S1 with cement, ferrous sulfate and quicklime to obtain a mixed slurry;
[0033] S3, mixing the mixed slurry in step S2 with aluminum powder to obtain casting slurry;
[0034] S4. Perform pouring, pre-curing, cutting and autoclaving curing of the pouring slurry to obtain an autoclaved aerated block.
[0035] The present invention utilizes the similar properties of heavy metal cadmium and calcium, and by setting an autoclaved curing step, cadmium ions react with silicate during the autoclaved curing process to form cadmium metasilicate or cadmium silicate, which is solidified into hydrogarnet and In tober mullite crystals, cadmium ions can replace part of the calcium element to f...
Embodiment 1
[0049] 1. Material selection: the water content of refined polluted acid slag is 35.0% by mass, the mass percentage of calcium sulfate is 30.0%; the mass percentage of silicon dioxide in fly ash is 47.0%, and the mass percentage of alumina is 27.5% %, calcium oxide mass percentage content is 4.5%, iron oxide mass percentage content is 3.0%; calcium oxide content in quicklime is 85%; hydrated ferrous sulfate is industrial grade, hydrated ferrous sulfate content is 95%; ordinary silicate cement.
[0050] 2. Add fly ash and water to the ball mill according to the mass percentage of fly ash (already contains 5% water): water ratio of 57:43, and carry out wet grinding or mixing to control the particle fineness, and more than 90% of the particles are over 180 Add dirty acid residue, at room temperature, under 150 rpm, stir for 2.0 hours, and prepare a siliceous slurry for subsequent use;
[0051] 3. Heat the siliceous slurry to 42°C, then add cement, hydrated ferrous sulfate, and q...
Embodiment 2
[0058] 1. Material selection: the water content of refined polluted acid slag is 35.0% by mass, the mass percentage of calcium sulfate is 30.0%; the mass percentage of silicon dioxide in fly ash is 47.0%, and the mass percentage of alumina is 27.5% %, calcium oxide mass percentage content is 4.5%, iron oxide mass percentage content is 3.0%; calcium oxide content in quicklime is 85%; hydrated ferrous sulfate is industrial grade, hydrated ferrous sulfate content is 95%; ordinary silicate cement.
[0059] 2. Put fly ash and water into the ball mill according to the mass percentage of fly ash: water ratio of 57:43 for wet grinding or mixing, control the particle fineness, more than 90% of the particles pass 180 mesh, add dirty acid slag, room temperature Under 150 rpm, stir for 3.0 hours to prepare a siliceous slurry for subsequent use;
[0060] 3. Heat the siliceous slurry to 40°C, then add cement, hydrated ferrous sulfate, and quicklime, and stir and mix for 1.0 minute to obtai...
PUM
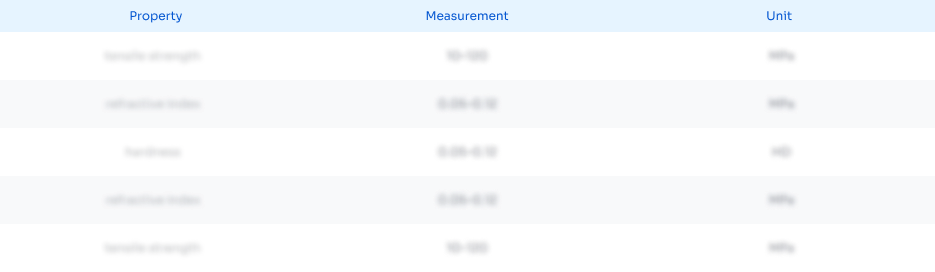
Abstract
Description
Claims
Application Information

- Generate Ideas
- Intellectual Property
- Life Sciences
- Materials
- Tech Scout
- Unparalleled Data Quality
- Higher Quality Content
- 60% Fewer Hallucinations
Browse by: Latest US Patents, China's latest patents, Technical Efficacy Thesaurus, Application Domain, Technology Topic, Popular Technical Reports.
© 2025 PatSnap. All rights reserved.Legal|Privacy policy|Modern Slavery Act Transparency Statement|Sitemap|About US| Contact US: help@patsnap.com