Production method for 2,3,3,3-tetra-fluoropropene
A technology of tetrafluoropropene and its manufacturing method, which is applied in chemical instruments and methods, preparation of halogenated hydrocarbons, organic chemistry, etc., can solve problems such as unrealistic, high VdF ratio, insufficient supply of raw material components, etc., and achieve great effect, cost reduction effect
- Summary
- Abstract
- Description
- Claims
- Application Information
AI Technical Summary
Problems solved by technology
Method used
Image
Examples
Embodiment 1
[0078] use figure 1 In the reaction apparatus shown, the raw material gas composed of R22 and R40 was as follows to obtain crude HFO-1234yf.
[0079] R40 was continuously introduced into the stainless steel tube preheater 2a in the electric furnace whose temperature in the furnace was set to 500°C, and R40 was heated to 500°C. In addition, R22 was continuously introduced into a preheater 3a made of stainless steel tubes in an electric furnace whose temperature in the furnace was set to 500°C, and R22 was heated to 500°C.
[0080] The heated steam (steam) was supplied at 0.04 MPa to the reactor 1 whose inner temperature was controlled at 850° C. by the heating steam generator 4 a which is an electric furnace whose inner temperature was set at 850° C. Further, the raw material gas components (R40 and R22) heated in advance and adjusted to the above-mentioned temperature are supplied to the reactor 1 under the following conditions; , and with respect to the total gas supply amo...
Embodiment 2~4
[0106] The reaction was carried out under the same conditions as in Example 1 except that the molar ratio (R40 / R22) of the supplied amount of R40 and the supplied amount of R22 was changed as shown in Table 1. Next, the gas of the reaction mixture taken out from the outlet of the reactor was treated in the same manner as in Example 1, and the obtained outlet gas was analyzed in the same manner as in Example 1. The results are shown in Table 1 together with the reaction conditions.
Embodiment 5
[0112] Same as Example 1, use figure 2 In the reaction apparatus shown, crude HFO-1234yf was obtained from the raw material gas composed of R22 and R40 as shown below.
[0113] R40 was continuously introduced into a stainless steel tube in an electric furnace whose temperature in the furnace was set to 600°C, and R40 was heated to 600°C. In addition, R22 was continuously introduced into a stainless steel tube in an electric furnace whose furnace temperature was set to 300°C, and R22 was heated to 300°C.
[0114] The raw material gas components (R40 and R22) heated in advance and adjusted to the above-mentioned temperature and steam (steam) heated by an electric furnace with the furnace temperature set at 750° C. were supplied to the reactor under the following conditions; The above conditions are: the molar ratio of the supply amount of the raw material components is set to R40 / R22=3, and the supply ratio of water vapor (water vapor / (R40+R22+water vapor) is expressed in volu...
PUM
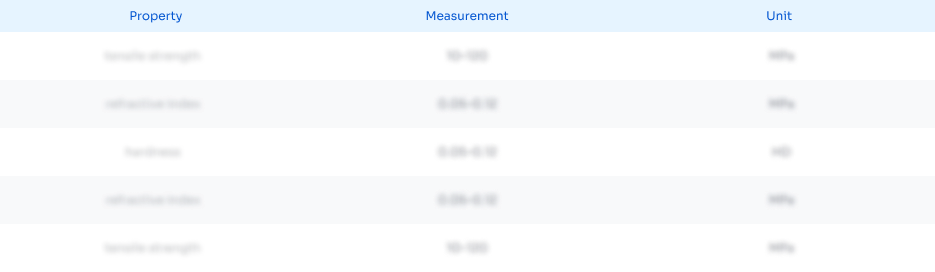
Abstract
Description
Claims
Application Information

- R&D
- Intellectual Property
- Life Sciences
- Materials
- Tech Scout
- Unparalleled Data Quality
- Higher Quality Content
- 60% Fewer Hallucinations
Browse by: Latest US Patents, China's latest patents, Technical Efficacy Thesaurus, Application Domain, Technology Topic, Popular Technical Reports.
© 2025 PatSnap. All rights reserved.Legal|Privacy policy|Modern Slavery Act Transparency Statement|Sitemap|About US| Contact US: help@patsnap.com