An adaptive frequency modulation dynamic vibration absorber
A dynamic vibration absorber and self-adaptive technology, used in springs/shock absorbers, vibration suppression adjustment, mechanical equipment, etc., can solve the problem of simple frequency modulation structure and reliability requirements, complex electromagnetic stiffness of auxiliary equipment, and easy nonlinearity. and other problems, to achieve the effect of flexible layout, high degree of versatility and smooth operation
- Summary
- Abstract
- Description
- Claims
- Application Information
AI Technical Summary
Problems solved by technology
Method used
Image
Examples
Embodiment Construction
[0025] The present invention will be described in detail below with reference to the accompanying drawings and examples.
[0026] as attached figure 1 As shown, it includes stepping motor 1, connecting rod assembly, adjusting mass 6, fixed mass 7, nut 8, stepping motor control system 4, elastic element 3, terminal 5, upper panel 15, lower bottom plate 2, straight line Bearing II16, linear bearing III18, connecting rod pin 17, turntable pin 19, pin nut 12 and casing 14, wherein the connecting rod assembly includes turntable 13, connecting rod 11, guide rod 9 and a linear bearing embedded in the casing I10;
[0027] Its overall connection relationship is as follows: the upper panel 15 and the lower base plate 2 seal the upper and lower open ends of the casing 14 to form a closed cavity, and the stepping motor 1 is fixed on the center of the lower base plate 2 and is located in the closed cavity. The motor control system 4 is fixed on the lower base plate 2 through the elastic ...
PUM
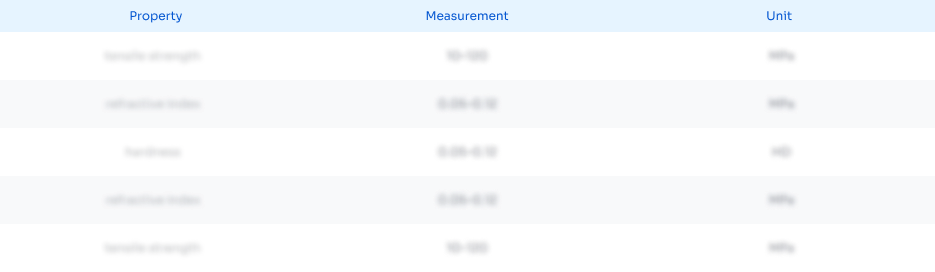
Abstract
Description
Claims
Application Information

- R&D
- Intellectual Property
- Life Sciences
- Materials
- Tech Scout
- Unparalleled Data Quality
- Higher Quality Content
- 60% Fewer Hallucinations
Browse by: Latest US Patents, China's latest patents, Technical Efficacy Thesaurus, Application Domain, Technology Topic, Popular Technical Reports.
© 2025 PatSnap. All rights reserved.Legal|Privacy policy|Modern Slavery Act Transparency Statement|Sitemap|About US| Contact US: help@patsnap.com