High pressure common rail forged piece of engine
A high-pressure common rail and engine technology, applied in the field of high-pressure common rail forgings for engines, can solve the problems of difficult to achieve ideal comprehensive mechanical properties, multiple production equipment and human resources, energy waste, etc., to shorten the production cycle and reduce production costs , the effect of reducing energy consumption
- Summary
- Abstract
- Description
- Claims
- Application Information
AI Technical Summary
Problems solved by technology
Method used
Image
Examples
Embodiment 1
[0027] The engine high-pressure common rail forging described in this embodiment includes a rail body with an axial passage, and a plurality of radial pipes forged together with the rail body; the material of the forging is low alloy steel, specifically the The content of C in the above-mentioned low alloy steel is 0.30wt%, the content of Si is 0.35wt%, the content of Mn is 0.72wt%, the content of Cr is 0.44wt%, the content of Mo is 0.15wt%, the content of V is 0.16 wt%, the content of Ti is 0.015wt%, the content of Al is 0.015wt%, the content of Ni is 0.12wt%, the content of P is 0.012wt%, the content of S is 0.010wt%, the balance is Fe and unavoidable of impurities. The smelting method of the low-alloy steel is prepared by the method of electric furnace + refining outside the furnace + vacuum degassing. The heat treatment of the high-pressure common rail forgings is realized by the forgings being processed in the rapid cooling zone, the stable zone and the slow cooling zone...
Embodiment 2
[0029] The engine high-pressure common rail forging described in this embodiment includes a rail body with an axial passage, and a plurality of radial pipes forged together with the rail body; the material of the forging is low alloy steel, specifically the The content of C in the low alloy steel is 0.35wt%, the content of Si is 0.25wt%, the content of Mn is 0.85wt%, the content of Cr is 0.48wt%, the content of Mo is 0.18wt%, and the content of V is 0.18wt%. wt%, the content of Ti is 0.015wt%, the content of Al is 0.015wt%, the content of Ni is 0.12wt%, the content of P is 0.012wt%, the content of S is 0.010wt%, the balance is Fe and unavoidable of impurities. The smelting method of the low-alloy steel is prepared by the method of electric furnace + refining outside the furnace + vacuum degassing. The heat treatment of the high-pressure common rail forgings is realized by the forgings being processed in the rapid cooling zone, the stable zone and the slow cooling zone. When ...
PUM
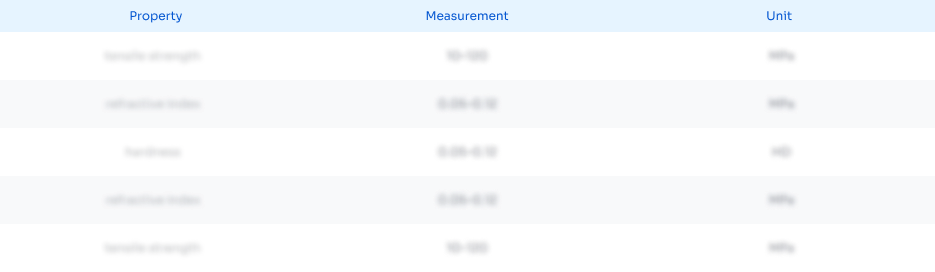
Abstract
Description
Claims
Application Information

- R&D
- Intellectual Property
- Life Sciences
- Materials
- Tech Scout
- Unparalleled Data Quality
- Higher Quality Content
- 60% Fewer Hallucinations
Browse by: Latest US Patents, China's latest patents, Technical Efficacy Thesaurus, Application Domain, Technology Topic, Popular Technical Reports.
© 2025 PatSnap. All rights reserved.Legal|Privacy policy|Modern Slavery Act Transparency Statement|Sitemap|About US| Contact US: help@patsnap.com