Epoxypropane purifying method
A technology of propylene oxide and purification method, applied in the direction of organic chemistry and the like, can solve the problems of low yield of propylene oxide and large loss of extractant, and achieve the effect of high extraction efficiency and good technical effect.
- Summary
- Abstract
- Description
- Claims
- Application Information
AI Technical Summary
Problems solved by technology
Method used
Image
Examples
Embodiment 1
[0048] The crude propylene oxide solution (stream 1) exchanges heat with the liquid in the solvent recovery tower (stream 5) to 80°C and enters the extractive distillation tower T-101. The extractive distillation tower uses n-octane as the extraction agent, and the solvent ratio of the extractive distillation tower (extraction The flow rate ratio of agent stream 6 to crude propylene oxide solution feed 1) is 4, deionized water (stream 12) is sprayed into the gas phase at the top of the tower, and oil-water separation operation is carried out in the tower top phase separator D-101 after condensation. There are multi-layer partitions in the phase vessel, and the separated oil layer (stream 8) is mixed with the recovered extractant (stream 6) as the reflux of the extractive distillation tower (stream 13), and the separated water layer (stream 9) enters the water washing tower T -103, the number of theoretical plates of the T101 column is 70, the operating pressure is controlled at...
Embodiment 2
[0060] The crude propylene oxide solution (stream 1) exchanges heat with the liquid in the solvent recovery tower (stream 3) to 70°C and enters the extractive distillation tower T-101. The extractive distillation tower uses n-heptane as the extraction agent, and the solvent ratio of the extractive distillation tower (extraction The flow rate ratio of agent stream 6 to crude propylene oxide solution feed 1) is 5:1, medium-pressure steam (stream 12) is injected into the gas phase at the top of the tower, and the oil-water separation operation is carried out in the top phase separator D-101 after condensation , there are multi-layer partitions in the phase separator, the separated oil layer (stream 8) is mixed with the recovered extractant (stream 6) as the reflux of the extractive distillation column (stream 13), and the separated water layer (stream 9) enters the water wash The theoretical plate number of tower T-103 and T101 is 75, the operating pressure is controlled at 200kPa...
PUM
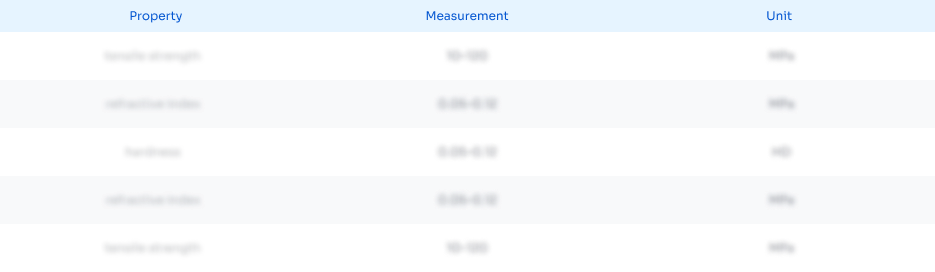
Abstract
Description
Claims
Application Information

- R&D Engineer
- R&D Manager
- IP Professional
- Industry Leading Data Capabilities
- Powerful AI technology
- Patent DNA Extraction
Browse by: Latest US Patents, China's latest patents, Technical Efficacy Thesaurus, Application Domain, Technology Topic, Popular Technical Reports.
© 2024 PatSnap. All rights reserved.Legal|Privacy policy|Modern Slavery Act Transparency Statement|Sitemap|About US| Contact US: help@patsnap.com