A kind of method for preparing isobutene by isobutane chlorination
A technology of isobutane and isobutene, which is applied in the direction of hydrocarbon production from halogen-containing organic compounds, can solve the problems of harsh hydrogenation reaction conditions, low selectivity of isobutene, and low conversion rate of isobutane, and achieve easy control of reaction conditions, Improvement of conversion rate and selectivity and reduction of running cost
- Summary
- Abstract
- Description
- Claims
- Application Information
AI Technical Summary
Problems solved by technology
Method used
Image
Examples
Embodiment 1
[0039] Embodiment 1~20 adopts attached figure 1 The process, wherein the following examples 1 to 9 are examples of chlorination reactions with different parameters, and examples 10 to 20 are examples of de-HCL reactions with different parameters.
[0040] Chlorination reaction:
[0041] Example 1:
[0042] Raw material isobutane with a purity of more than 99% and circulating isobutane are preheated to 60°C by the feed heater, and enter the photochlorination reactor together with chlorine gas. The molar ratio of starting materials is isobutane: chlorine gas is 6:1 , under the conditions of 60°C, normal pressure, and 15W ultraviolet light irradiation, the chlorination reaction was carried out. During the reaction process, the feed rate of fresh raw material isobutane was controlled at 60L / h (2.68mol / h), and the feed rate of chlorine gas was 60L / h. h (2.68mol / h), the molar ratio of isobutane to chlorine in the reactor is maintained at 6:1, and the reflux of isobutane is control...
Embodiment 10
[0051] The isobutane monochloride obtained by the chlorination reaction enters the de-HCL reactor equipped with 0.581kg (active component Cu2+0.554mol) catalyst at 0.250Kg / h (2.7mol / h), and the isobutane monochloride The molar ratio with the catalyst is 4.87:1, and the de-HCL reaction is carried out at 140°C under normal pressure to obtain a mixture containing isobutene, HCL and unreacted isobutane monochloride, which is cooled and separated;
[0052] The separated liquid unreacted isobutane-chloride is recycled back to the HCL removal reaction system. After the gaseous material isobutene and HCL are pressurized, they enter the hydrochloric acid absorption device to remove HCL. After the isobutene is washed with alkali, the product isobutene (1.67mol / h) is obtained. .
[0053] In the HCL removal reaction, the conversion rate of isobutane-chloride is 62%, and the generated product is pure isobutene, and the content of isobutene is greater than 99% according to chromatographic a...
PUM
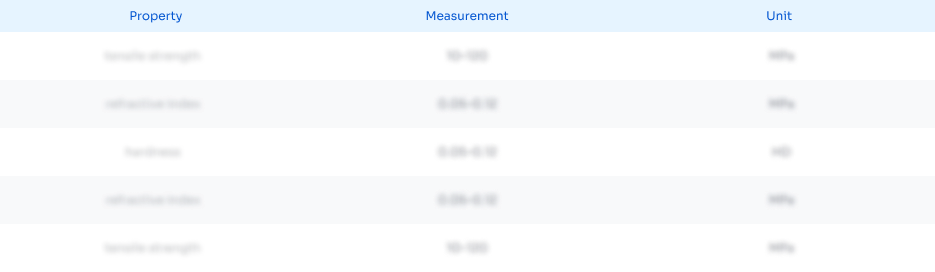
Abstract
Description
Claims
Application Information

- Generate Ideas
- Intellectual Property
- Life Sciences
- Materials
- Tech Scout
- Unparalleled Data Quality
- Higher Quality Content
- 60% Fewer Hallucinations
Browse by: Latest US Patents, China's latest patents, Technical Efficacy Thesaurus, Application Domain, Technology Topic, Popular Technical Reports.
© 2025 PatSnap. All rights reserved.Legal|Privacy policy|Modern Slavery Act Transparency Statement|Sitemap|About US| Contact US: help@patsnap.com