Aqueous organosilicone-modified alkyd resin and preparing method thereof
A technology of alkyd resin and silicone, which is applied in the direction of polyester coatings and coatings, can solve the problems of low storage performance of alkyd resin, high reaction temperature, easy caking gel, etc., and achieve low viscosity and low product cost. Low, full film effect
- Summary
- Abstract
- Description
- Claims
- Application Information
AI Technical Summary
Problems solved by technology
Method used
Image
Examples
Embodiment 1
[0037] Under the condition of nitrogen protection, add 50.05g of linseed oil, 13.01g of glycerin and 0.038g of alcoholysis catalyst LiOH to the reaction vessel, first raise the temperature to 180°C at a rate of 3°C / min, and then increase the temperature at a rate of 40°C / h Raise the temperature to 220°C for alcoholysis reaction; when the tolerance of ethanol with a mass concentration of 87% reaches 1:3, start to cool down; cool down to 160°C, add 23.38g of phthalic anhydride, 5.06g2 , 2-dimethylol propionic acid, 0.022g esterification catalyst BC-98 and consumption are the reflux solvent xylene of total charging capacity 5% (total charging capacity is unsaturated fatty oil, polyhydric alcohol, polybasic acid and 2,2 - the total content of dimethylolpropionic acid), and install a water separator to remove the water generated by the entire esterification reaction (theoretical water output is 2.44g), keep it warm for 1h, and slowly heat up to 220°C at a speed of 20°C / h; Stop heat...
Embodiment 2
[0039]Under the condition of nitrogen protection, 59.85g of soybean oil, 12.59g of pentaerythritol and 0.040g of alcoholysis catalyst CaO were added to the reaction vessel, and the temperature was first raised to 180°C at a rate of 3°C / min, and then at a rate of 60°C / h Raise the temperature to 250°C for alcoholysis reaction; when the tolerance of ethanol with a mass concentration of 87% reaches 1:4, start to cool down; cool down to 200°C, add 21.21g of phthalic anhydride, 2.24g of cis Butenedioic anhydride, 5.45g2, 2-dimethylol propionic acid, 0.088g esterification catalyst BC-98 and consumption are the reflux solvent xylene of 10% of total charging amount, install water trap simultaneously and remove the esterification reaction to generate Water (theoretical water output is 2.40g), slowly heat up to 260°C at a rate of 30°C / h; stop heating when the acid value of the system is 80mgKOH / g, and start to cool down to 80°C at a rate of 15 drops per minute 21.58 g of methyltriethoxys...
Embodiment 3
[0042] Under the condition of nitrogen protection, add 40.05g of linseed oil, 10.00g of tung oil, 8.78g of 1,1,1-trimethylolpropane and 0.022g of alcoholysis catalyst LiOH to the reaction vessel, first at a rate of 3°C / min Raise the temperature to 180°C, and then raise the temperature to 230°C at a rate of 50°C / h for alcoholysis; when the tolerance of ethanol with a mass concentration of 87% reaches 1:6, start to cool down; Add 21.43g of phthalic anhydride, 2.07g of nadic anhydride (cis-3,6-endomethylene-1,2,3,6-tetrahydrophthalic anhydride), 5.29g of 2,2 -Dimethylol propionic acid, 0.058g esterification catalyst BC-98 and consumption are the reflux solvent dimethylbenzene of 8% of total charging capacity, install water separator simultaneously and remove the water that esterification generates (theoretical water yield is 2.36g) , slowly warming up to 240°C at a rate of 10°C / h; stop heating when the acid value of the system is 60mgKOH / g, start to cool down, drop the temperatur...
PUM
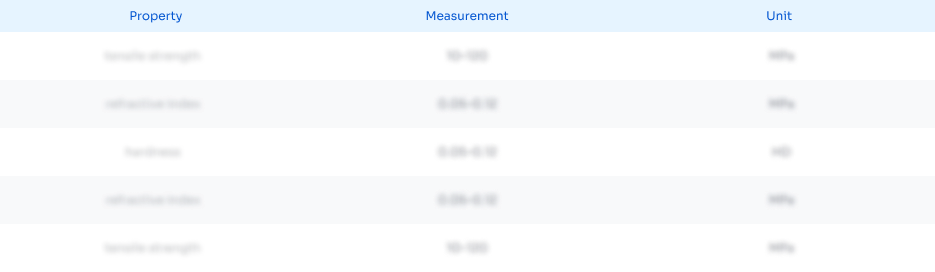
Abstract
Description
Claims
Application Information

- R&D
- Intellectual Property
- Life Sciences
- Materials
- Tech Scout
- Unparalleled Data Quality
- Higher Quality Content
- 60% Fewer Hallucinations
Browse by: Latest US Patents, China's latest patents, Technical Efficacy Thesaurus, Application Domain, Technology Topic, Popular Technical Reports.
© 2025 PatSnap. All rights reserved.Legal|Privacy policy|Modern Slavery Act Transparency Statement|Sitemap|About US| Contact US: help@patsnap.com