Method for preparing steelmaking flux from refining waste slag under thermal state
A technology for refining waste slag and refining slag, which is applied in the direction of manufacturing converters, improving process efficiency, recycling technology, etc., can solve the problems of large amount of refining slag and high CaO content, and achieves reduction of processing costs, energy saving, and difficulty in pulverization. Effect
- Summary
- Abstract
- Description
- Claims
- Application Information
AI Technical Summary
Problems solved by technology
Method used
Examples
Embodiment 1
[0022] Example 1: A high-Al and low-Si type hot refining waste slag was transferred from the LF furnace ladle to the melting furnace for hot desulfurization by hoisting. The composition of the waste slag is shown in Table 1.
[0023] Table 1 The content of each component of the refining waste slag in Example 1 Unit: %
[0024] Fe 2 o 3 CaO SiO 2 MgO Al 2 o 3 SO 3 BaO SrO ZrO 2 2.94 37.37 6.58 3.37 46.09 1.16 0.025 0.035 0.014
[0025] Under the condition of 1400°C, oxygen was introduced, the oxygen partial pressure was 2atm, and the reaction time was 40mim. After the desulfurization reaction is completed, the SO in the slag 3 Content decreased from 1.16 to 0.04. Then continue to mix CaO and CaF into the slag under the condition of 1400°C2 , the dosage is based on the preparation of 1000 kg pre-melted refining slag, refining waste slag: 760 kg, CaO: 210kg, CaF 2 : 30 kg, after reacting for 60 minutes, cool the slag and break...
Embodiment 2
[0026] Example 2: A high-Al and low-Si hot refining waste slag was transferred from the LF furnace ladle to the melting furnace for hot desulfurization by hoisting. The composition of the waste slag is shown in Table 2.
[0027] Table 2 Contents of each component of refining waste residue in Example 2 Unit: %
[0028] Fe 2 o 3 CaO SiO 2 MgO al 2 o 3 SO 3 BaO SrO ZrO 2 3.53 52.86 5.71 4.88 23.36 2.18 0.09 0.05 0.02
[0029] Under the condition of 1300°C, oxygen was introduced, the oxygen partial pressure was 2atm, and the reaction time was 60mim. After the desulfurization reaction is completed, the SO in the slag 3 Content decreased from 2.18 to 0.02. Then continue to mix CaO and CaF into the slag under the condition of 1300°C 2 , the dosage is based on the preparation of 1000 kg pre-melted refining slag agent, refining waste slag: 800 kg, CaO: 50 kg, Al 2 o 3 : 130 kg, CaF 2 : 20 kg, after reacting for 60 minutes, cool th...
Embodiment 3
[0031] Example 3: Transfer a high-Al refining slag waste from the ladle of the LF furnace to the melting furnace by hoisting for thermal desulfurization reaction. The composition of the waste slag is shown in Table 3.
[0032] Table 3 Contents of each component of refining waste residue in Example 3 Unit: %
[0033] Fe 2 o 3 CaO SiO 2 MgO al 2 o 3 SO 3 BaO SrO ZrO 2 1.74 52.86 12.10 4.48 23.54 2.11 0.025 0.035 0.014
[0034] Under the condition of 1400°C, oxygen was introduced, the oxygen partial pressure was 2atm, and the reaction time was 50mim. After the desulfurization reaction is completed, the SO in the slag 3 Content decreased from 2.11 to 0.05. Then continue to mix Fe into the slag under the condition of 1400°C 2 o 3 . The dosage is based on the preparation of 1000 kg converter slagging flux, refining waste slag: 950 kg, Fe 2 o 3 : 50 kg, after reacting for 40 minutes, cool the slag and break it to 3-8mm to ge...
PUM
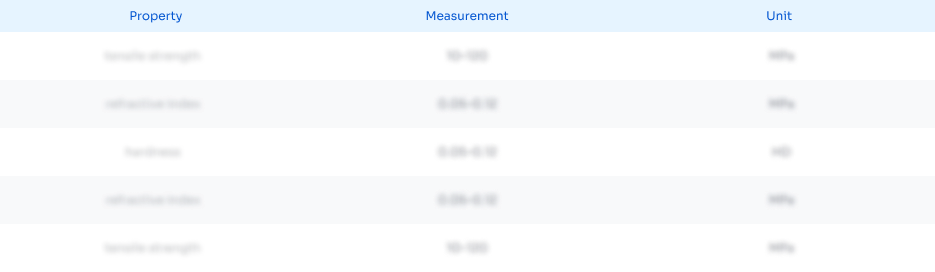
Abstract
Description
Claims
Application Information

- R&D
- Intellectual Property
- Life Sciences
- Materials
- Tech Scout
- Unparalleled Data Quality
- Higher Quality Content
- 60% Fewer Hallucinations
Browse by: Latest US Patents, China's latest patents, Technical Efficacy Thesaurus, Application Domain, Technology Topic, Popular Technical Reports.
© 2025 PatSnap. All rights reserved.Legal|Privacy policy|Modern Slavery Act Transparency Statement|Sitemap|About US| Contact US: help@patsnap.com