Energy-saving and high-efficiency plastic granulator
A granulator, high-efficiency technology, applied in the field of plastic machinery, can solve the problems of hindering the reasonable transfer of heat, insufficient scraper design, unstable working process, etc., to facilitate the dispersion and transfer of heat, avoid local overheating of materials, The effect of highlighting substantive features
- Summary
- Abstract
- Description
- Claims
- Application Information
AI Technical Summary
Problems solved by technology
Method used
Image
Examples
Embodiment Construction
[0023]As shown in the figure, the energy-saving and high-efficiency plastic granulator of the present invention includes a feed screw 5, a scraper 11, a feed barrel 2 arranged up and down, a feed barrel 7 and an extrusion die barrel 9, and the feed screw 5 is placed on the feed barrel 7. The inner rotation setting is driven by the main motor 15, the main motor 15 is located on the base 14, the upper end of the feeding screw 5 extends into the feeding barrel 2, the top of the feeding screw 5 is fixedly installed with the mixing paddle 4, the extrusion die barrel 9 and the corresponding The mold barrel top plate 8 and the mold barrel bottom plate 12 surround the granulation extrusion chamber 25 under the outlet of the feeding cylinder 7 together, and the scraper 11 is rotated in the granulation extrusion chamber 25 and is fixedly connected with the feeding screw 5. The upper surface of the scraper 11 is close to the mold cylinder top plate 8, the lower surface of the scraper 11 i...
PUM
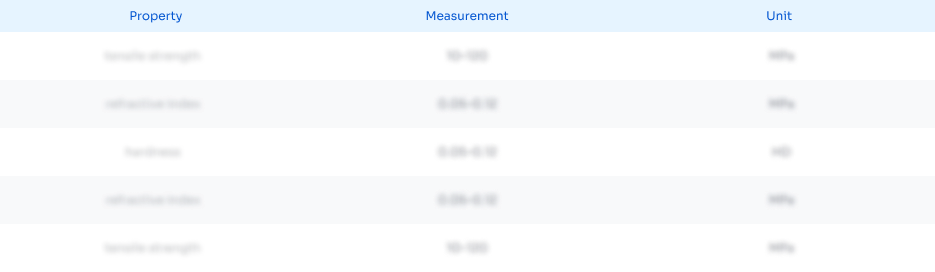
Abstract
Description
Claims
Application Information

- R&D
- Intellectual Property
- Life Sciences
- Materials
- Tech Scout
- Unparalleled Data Quality
- Higher Quality Content
- 60% Fewer Hallucinations
Browse by: Latest US Patents, China's latest patents, Technical Efficacy Thesaurus, Application Domain, Technology Topic, Popular Technical Reports.
© 2025 PatSnap. All rights reserved.Legal|Privacy policy|Modern Slavery Act Transparency Statement|Sitemap|About US| Contact US: help@patsnap.com