Production method of calcined kaolin for glass fibers
A technology for calcining kaolin and a production method, applied in the field of inorganic materials, can solve the problems of high COD value, unstable quality and high mullite phase content of kaolin used for glass fiber, so as to reduce energy consumption, reduce production cost and increase output Effect
- Summary
- Abstract
- Description
- Claims
- Application Information
AI Technical Summary
Problems solved by technology
Method used
Image
Examples
Embodiment 1
[0046] The kaolin raw materials include: by mass percentage, 20% of 1# kaolin (rock), 50% of 2# kaolin (rock) and 30% of 3# kaolin (rock).
[0047] The composition content of 1# kaolin (rock) is as follows: the following are mass percentages
[0048]
[0049] The composition content of 2# kaolin (rock) is as follows:
[0050]
[0051] The composition content of 3# kaolin (rock) is as follows:
[0052]
[0053] 1) Break the above three kinds of kaolin raw materials into small pieces less than 100mm, put them into their respective silos, and transport them to the upper material hopper of the fine crushing equipment with a metering belt, mix the small pieces and transport them to the rollers The machine is finely broken into granules below 10mm, and the granules enter the ball mill or vertical mill to be ground into 500-mesh fine powder.
[0054] 2) The fine powder enters the three-stage continuous cyclone preheating system. The preheating temperature of the first-stag...
Embodiment 2
[0057] The kaolin raw material is the same as that used in Example 1. Among them, 1# kaolin (rock) 20%, 2# kaolin (rock) 60% and 3# kaolin (rock) 20%.
[0058] 1) Break the above three kinds of kaolin raw materials into small pieces less than 100mm, put them into their respective silos, and transport them to the upper material hopper of the fine crushing equipment with a metering belt, mix the small pieces and transport them to the rollers The machine is finely broken into granules below 10mm, and the granules enter the ball mill or vertical mill to be ground into 300-mesh fine powder.
[0059] 2) The fine powder enters the three-stage continuous cyclone preheating system. The preheating temperature of the first-stage cyclone is 300°C, the preheating temperature of the second-stage cyclone is 380°C, and the preheating temperature of the third-stage cyclone is 460°C. Control the preheating time so that the loss on ignition of the intermediate product from the preheating cyclon...
Embodiment 3
[0062] The kaolin raw material is the same as that used in Example 1. Among them, 1# kaolin (rock) 20%, 2# kaolin (rock) 50% and 3# kaolin (rock) 30%.
[0063] 1) Break the above three kinds of kaolin raw materials into small pieces less than 100mm, put them into their respective silos, and transport them to the upper material hopper of the fine crushing equipment with a metering belt, mix the small pieces and transport them to the rollers The machine is finely broken into granules below 10mm, and the granules enter the ball mill or vertical mill to be ground into 1250 mesh fine powder.
[0064] 2) The fine powder enters the 3-stage continuous cyclone preheating system. The preheating temperature of the first-stage cyclone is 425°C, the preheating temperature of the second-stage cyclone is 500°C, and the preheating temperature of the third-stage cyclone is 600°C. Control the preheating time so that the loss on ignition of the intermediate product from the preheating cyclone i...
PUM
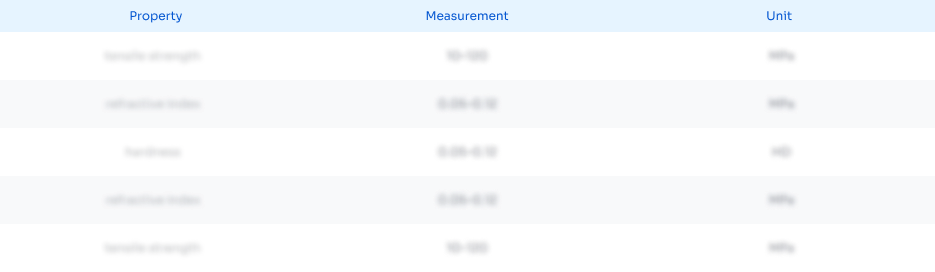
Abstract
Description
Claims
Application Information

- R&D Engineer
- R&D Manager
- IP Professional
- Industry Leading Data Capabilities
- Powerful AI technology
- Patent DNA Extraction
Browse by: Latest US Patents, China's latest patents, Technical Efficacy Thesaurus, Application Domain, Technology Topic, Popular Technical Reports.
© 2024 PatSnap. All rights reserved.Legal|Privacy policy|Modern Slavery Act Transparency Statement|Sitemap|About US| Contact US: help@patsnap.com