Processing technology for improving yarn shrinkage rate of microcapsule fragrant fabric tapes
A processing technology and microcapsule technology, which is applied in the processing of textile materials, textiles and papermaking, liquid/gas/steam textile material processing, etc., can solve the problems of active monomers easily reacting with core materials, etc., and achieve improved shrinkage, Soft to the touch, pure shade effect
- Summary
- Abstract
- Description
- Claims
- Application Information
AI Technical Summary
Problems solved by technology
Method used
Examples
specific Embodiment 1
[0021] A processing technology for improving the yarn shrinkage of microcapsule aromatic webbing, comprising the steps of:
[0022] (1) Yarn setting: put the polyester yarn into a dry steamer for dry steaming, the temperature of dry steaming is 110°C, and the time is 21 minutes;
[0023] (2) Loosening: Loosening the shaped polyester yarn;
[0024] (3) Dyeing: After adding microcapsule aromatic finishing agent and environmentally friendly acrylic soft adhesive, and adding auxiliary agents and dyes to the dyeing solution, soak the polyester yarn at a water temperature of 30°C for 5 minutes, and then the temperature is at After the rate of 2.5°C / min reaches 80°C, wash with water for 5 minutes, then raise the temperature to 115°C at a rate of 1.0°C / min, after washing for 5 minutes, increase the temperature to 130°C at a rate of 0.8°C / min, then wash with water for 30 minutes ;Finally, the water temperature drops to 80°C;
[0025] (4) Post-treatment: wash the dyed yarn with water ...
specific Embodiment 2
[0027] A processing technology for improving the yarn shrinkage of microcapsule aromatic webbing, comprising the steps of:
[0028] (1) Yarn setting: put the polyester yarn into a dry steamer for dry steaming, the temperature of dry steaming is 145°C, and the time is 36 minutes;
[0029] (2) Loosening: Loosening the shaped polyester yarn;
[0030] (3) Dyeing: After adding microcapsule aromatic finishing agent and environmentally friendly acrylic soft adhesive, and adding auxiliary agents and dyes to the dyeing solution, soak the polyester yarn at a water temperature of 30°C for 5 minutes, and then the temperature is at After the rate of 2.5°C / min reaches 80°C, wash with water for 5 minutes, then raise the temperature to 115°C at a rate of 1.0°C / min, after washing for 5 minutes, increase the temperature to 130°C at a rate of 0.8°C / min, then wash with water for 30 minutes ;Finally, the water temperature drops to 80°C;
[0031] (4) Post-treatment: wash the dyed yarn with water ...
specific Embodiment 3
[0033] A processing technology for improving the yarn shrinkage of microcapsule aromatic webbing, comprising the steps of:
[0034] (1) Yarn setting: put the polyester yarn into a dry steamer for dry steaming, the temperature of dry steaming is 130°C, and the time is 30 minutes;
[0035] (2) Loosening: Loosening the shaped polyester yarn;
[0036] (3) Dyeing: After adding microcapsule aromatic finishing agent and environmentally friendly acrylic soft adhesive, and adding auxiliary agents and dyes to the dyeing solution, soak the polyester yarn at a water temperature of 30°C for 5 minutes, and then the temperature is at After the rate of 2.5°C / min reaches 80°C, wash with water for 5 minutes, then raise the temperature to 115°C at a rate of 1.0°C / min, after washing for 5 minutes, increase the temperature to 130°C at a rate of 0.8°C / min, then wash with water for 30 minutes ;Finally, the water temperature drops to 80°C;
[0037] (4) Post-treatment: wash the dyed yarn with water ...
PUM
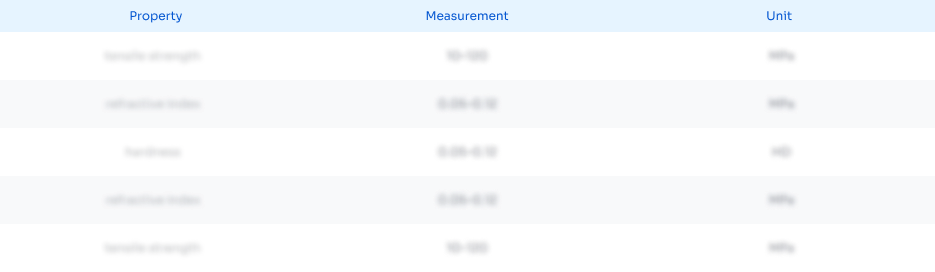
Abstract
Description
Claims
Application Information

- Generate Ideas
- Intellectual Property
- Life Sciences
- Materials
- Tech Scout
- Unparalleled Data Quality
- Higher Quality Content
- 60% Fewer Hallucinations
Browse by: Latest US Patents, China's latest patents, Technical Efficacy Thesaurus, Application Domain, Technology Topic, Popular Technical Reports.
© 2025 PatSnap. All rights reserved.Legal|Privacy policy|Modern Slavery Act Transparency Statement|Sitemap|About US| Contact US: help@patsnap.com