Method for preparing vanadium dioxide film
A technology of vanadium dioxide and thin film, which is applied in the field of vanadium dioxide thin film preparation of metal vanadium or low-valent vanadium oxidation annealing, can solve the problems of difficulty, no control of annealing atmosphere, poor repeatability, etc., and achieve process compatibility, excellent performance, good repeatability
- Summary
- Abstract
- Description
- Claims
- Application Information
AI Technical Summary
Problems solved by technology
Method used
Image
Examples
Embodiment 1
[0023] In this embodiment, float glass is used as a substrate, and a metal vanadium film is plated on its surface, then annealed in a vacuum tube annealing furnace to form a vanadium dioxide film, and then the performance of the film is tested. Wherein the annealing oxygen gas pressure is 18Pa, and concrete implementation steps are as follows:
[0024] 1 Substrate cleaning. Put the glass substrate in alcohol for 10 minutes to remove oil on the surface of the substrate. After ultrasonic cleaning, take it out quickly, dry it with nitrogen, and put it into the coating chamber.
[0025] 2 Plating 50nm metal vanadium thin film. The vanadium target used in the coating system is a 320×140mm planar target with a purity of 99.99%. The sputtering process gas is argon with a purity of 99.999%. System base vacuum is 1×10 -3 Pa. During sputter coating, adjust the argon flow rate to 50sccm, and the system pressure is 0.22Pa at this time; 3. Set the sputtering power to 500W, and the spu...
Embodiment 2
[0031] In this embodiment, float glass is used as a substrate, and a metal vanadium film is plated on its surface, then annealed in a vacuum tube annealing furnace to form a vanadium dioxide film, and then the performance of the film is tested. Wherein the annealing oxygen gas pressure is 33Pa, and concrete implementation steps are as follows:
[0032] 1 Substrate cleaning. Put the glass substrate in alcohol for 10 minutes to remove oil on the surface of the substrate. After ultrasonic cleaning, take it out quickly, dry it with nitrogen, and put it into the coating chamber.
[0033] 2 Plating 50nm metal vanadium thin film. The vanadium target used in the coating system is a 320×140mm planar target with a purity of 99.99%. The sputtering process gas is argon with a purity of 99.999%. System base vacuum is 1×10 -3 Pa. During sputter coating, adjust the argon flow rate to 50sccm, and the system pressure is 0.22Pa at this time; set the sputtering power to 500W, and the sputte...
Embodiment 3
[0039] In this embodiment, float glass is used as a substrate, and a metal vanadium film is plated on its surface, then annealed in a vacuum tube annealing furnace to form a vanadium dioxide film, and then the performance of the film is tested. The specific implementation steps are as follows:
[0040] 1 Substrate cleaning. Put the glass substrate in alcohol for 10 minutes to remove oil on the surface of the substrate. After ultrasonic cleaning, take it out quickly, dry it with nitrogen, and put it into the coating chamber.
[0041] 2 Plating 50nm metal vanadium thin film. The vanadium target used in the coating system is a 320×140mm planar target with a purity of 99.99%. The sputtering process gas is argon with a purity of 99.999%. System base vacuum is 1×10 -3 Pa. During sputter coating, adjust the argon flow rate to 50sccm, and the system pressure is 0.22Pa at this time; set the sputtering power to 500W, and the sputtering voltage is 338V at this time; take out the fil...
PUM
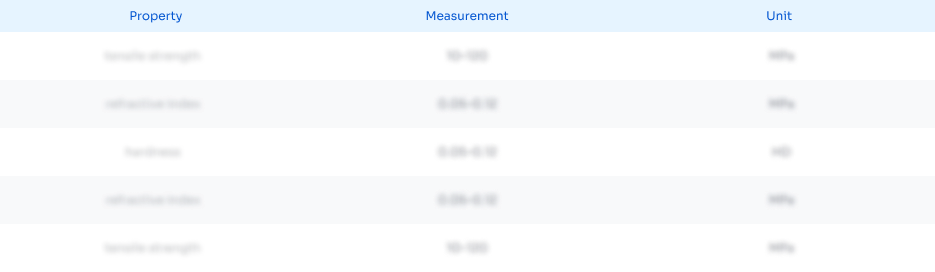
Abstract
Description
Claims
Application Information

- R&D
- Intellectual Property
- Life Sciences
- Materials
- Tech Scout
- Unparalleled Data Quality
- Higher Quality Content
- 60% Fewer Hallucinations
Browse by: Latest US Patents, China's latest patents, Technical Efficacy Thesaurus, Application Domain, Technology Topic, Popular Technical Reports.
© 2025 PatSnap. All rights reserved.Legal|Privacy policy|Modern Slavery Act Transparency Statement|Sitemap|About US| Contact US: help@patsnap.com