Preparation method of polyamide reverse osmosis membrane containing amphoteric carboxymethylcellulose sodium complex
A technology of sodium carboxymethyl cellulose and reverse osmosis membrane, applied in the field of preparation of polyamide reverse osmosis membrane, to achieve good pollution resistance, high water permeability and pollution resistance, and improve transmission efficiency
- Summary
- Abstract
- Description
- Claims
- Application Information
AI Technical Summary
Problems solved by technology
Method used
Examples
preparation example Construction
[0015] The preparation method of the polyamide reverse osmosis membrane containing amphoteric sodium carboxymethyl cellulose complex comprises the steps:
[0016] (1) Dissolve 10-30 parts by mass of zwitterionic monomers and 5-10 parts by mass of cationic monomers in an aqueous solution of 50-200 parts by mass, blow nitrogen into it, and add 0.1-1 parts by mass of water-soluble initiator , at 40-60 o Polymerize at C for 6-12 hours, precipitate the polymer with acetone, and wash it several times to obtain an amphoteric cationic polymer, which is vacuum-dried for later use;
[0017] (2) Dissolve 1-3 parts by mass of sodium carboxymethylcellulose and 0.5-2 parts by mass of amphoteric cationic polymer in 100-500 parts by mass of acidic aqueous solution, and then add the acidic aqueous solution of amphoteric cationic polymer dropwise Carry out ionic cross-linking in the acidic aqueous solution of sodium carboxymethyl cellulose, after precipitation, wash with deionized water severa...
Embodiment 1
[0022] 10 g of 3-[N,N-dimethyl-[2-(2-methylprop-2-enoyloxy)ethyl]ammonium]propane-1-sulfonic acid inner salt and 5 g of methacrylic acid Dissolve acyloxyethyltrimethylammonium chloride in 50 g of aqueous solution, pass through nitrogen, add 0.1 g of potassium persulfate and sodium bisulfite (mass ratio is 1:1), at 40 o C was polymerized for 12 hours, precipitated with acetone, washed several times, and dried in vacuum to obtain an amphoteric cationic polymer; 1 g of sodium carboxymethylcellulose and 0.5 g of amphoteric cationic polymer were dissolved in 100 g of 0.01wt% hydrochloric acid aqueous solution, then the amphoteric cationic polymer acidic aqueous solution is added dropwise in the sodium carboxymethyl cellulose acidic aqueous solution to carry out ion cross-linking, after precipitation, washed with deionized water several times, at 40 o C was dried for 16 hours to obtain the amphoteric sodium carboxymethylcellulose complex; then the above-mentioned 0.2 g complex was a...
Embodiment 2
[0024] 30 g of 3-[N,N-dimethyl-[2-(2-methylprop-2-enoyloxy)ethyl]ammonium]propane-1-sulfonic acid inner salt and 10 g of methacrylic acid Dissolve acyloxyethyltrimethylammonium chloride in 200 g of aqueous solution, pass through nitrogen, add 1 g of potassium persulfate and sodium bisulfite (mass ratio: 1:1), at 60 o C was polymerized for 6 hours, precipitated with acetone, washed several times, and vacuum-dried to obtain an amphoteric cationic polymer; 3 g of sodium carboxymethylcellulose and 2 g of amphoteric cationic polymer were dissolved in 500 g of 0.1wt% hydrochloric acid aqueous solution, and then the amphoteric cationic polymer acidic aqueous solution is added dropwise in the sodium carboxymethyl cellulose acidic aqueous solution to carry out ion cross-linking, after precipitation, washed with deionized water several times, at 60 o C was dried for 8 hours to obtain the amphoteric sodium carboxymethylcellulose complex; then the complex of the above 1 g was added to 500...
PUM
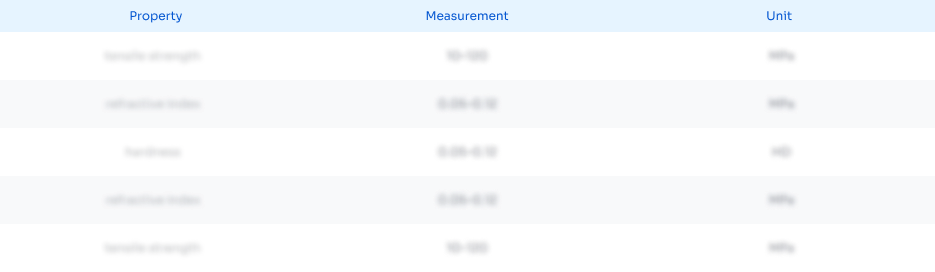
Abstract
Description
Claims
Application Information

- R&D Engineer
- R&D Manager
- IP Professional
- Industry Leading Data Capabilities
- Powerful AI technology
- Patent DNA Extraction
Browse by: Latest US Patents, China's latest patents, Technical Efficacy Thesaurus, Application Domain, Technology Topic, Popular Technical Reports.
© 2024 PatSnap. All rights reserved.Legal|Privacy policy|Modern Slavery Act Transparency Statement|Sitemap|About US| Contact US: help@patsnap.com