Production method for diammonium hydrogen phosphate
A technology of diammonium hydrogen phosphate and a production method, which is applied in the direction of phosphate, phosphorus oxyacid, etc., can solve the problems of high production cost, long process route, and large energy consumption, and achieve short production cycle, short process flow, and low energy consumption. can low effect
- Summary
- Abstract
- Description
- Claims
- Application Information
AI Technical Summary
Problems solved by technology
Method used
Image
Examples
Embodiment 1
[0040] A production method of diammonium hydrogen phosphate, which is to use high-purity urea phosphate solution and ammonia for metathesis reaction, and control the pH value to 7.8, and the temperature is 50°C, stirring and reacting for 20 minutes to prepare the diammonium hydrogen phosphate product.
[0041] Specifically include the following steps:
[0042](1) Preparation of urea phosphate solution: the urea phosphate solid with a purity of 97% is sent into a dissolving tank, water is added and measured, heated to a temperature of 40° C., and under stirring conditions, stirring is carried out at a stirring speed of 60 r / min. After mixing evenly, prepare a saturated urea phosphate solution for use;
[0043] (2) Diammonium hydrogen phosphate is synthesized: the saturated urea phosphate solution prepared in step 1) is transported in the synthesis tank by a delivery pump, and ammonia is passed into it, and the mol ratio of ammonia and saturated urea phosphate is 2: 1. Control ...
Embodiment 2
[0047] A production method of diammonium hydrogen phosphate, which is to use high-purity urea phosphate solution and ammonia for metathesis reaction, and control the pH value to 8.2, the temperature is 80 DEG C, stirring and reacting for 60 minutes to prepare the diammonium hydrogen phosphate product.
[0048] Specifically include the following steps:
[0049] (1) Preparation of urea phosphate solution: the urea phosphate solid with a purity of 98% is sent into a dissolving tank, water is added and measured, heated to a temperature of 60° C., and under stirring conditions, stirring is carried out at a stirring speed of 80 r / min. After mixing evenly, prepare a saturated urea phosphate solution for use;
[0050] (2) diammonium hydrogen phosphate is synthesized: the saturated urea phosphate solution prepared in step 1) is transported in the synthesis tank by a delivery pump, and feeds ammonia thereinto, and the mol ratio of ammonia and saturated urea phosphate is 2.5: 1. Control...
Embodiment 3
[0054] A production method of diammonium hydrogen phosphate, which is to use high-purity urea phosphate solution and ammonia for metathesis reaction, and control the pH value to 8, and the temperature is 65° C., stirring and reacting for 40 minutes to prepare the diammonium hydrogen phosphate product.
[0055] Specifically include the following steps:
[0056] (1) Preparation of urea phosphate solution: the urea phosphate solid with a purity of 99% is sent into a dissolving tank, water is added and measured, heated to a temperature of 50° C., and under stirring conditions, stirring is carried out at a stirring speed of 70 r / min. After mixing evenly, prepare a saturated urea phosphate solution for use;
[0057] (2) diammonium hydrogen phosphate is synthesized: the saturated urea phosphate solution prepared in step 1) is transported in the synthesis tank by a delivery pump, and feeds ammonia thereinto, and the mol ratio of ammonia and saturated urea phosphate is 2.3: 1. Control...
PUM
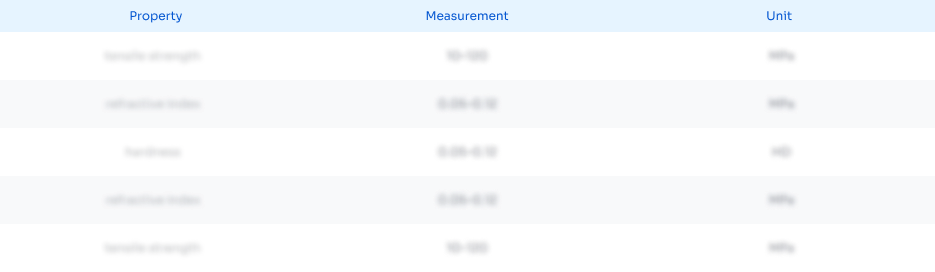
Abstract
Description
Claims
Application Information

- R&D
- Intellectual Property
- Life Sciences
- Materials
- Tech Scout
- Unparalleled Data Quality
- Higher Quality Content
- 60% Fewer Hallucinations
Browse by: Latest US Patents, China's latest patents, Technical Efficacy Thesaurus, Application Domain, Technology Topic, Popular Technical Reports.
© 2025 PatSnap. All rights reserved.Legal|Privacy policy|Modern Slavery Act Transparency Statement|Sitemap|About US| Contact US: help@patsnap.com