Method used for producing silane and trichlorosilane via reactive distillation
A technology of reactive distillation and trichlorosilane, which is applied in the direction of halosilane, silicon hydride, silicon halide compounds, etc., can solve the problems of difficult catalyst replacement, short service life of solid catalysts, inability to overcome defects, etc., and is suitable for large-scale industrialization Production, solve the difficulty of catalyst replacement, improve the effect of continuous operation capacity
- Summary
- Abstract
- Description
- Claims
- Application Information
AI Technical Summary
Problems solved by technology
Method used
Image
Examples
Embodiment 1
[0069]A mixed liquid catalyst of n-dodecylamine and aniline is used as a catalyst for the disproportionation reaction of trichlorosilane, wherein the mole fraction of n-dodecylamine liquid catalyst in the mixed liquid catalyst accounts for 80%, and the amount of catalyst is 5% of the total mass of trichlorosilane .
[0070] The operating pressure of the disproportionation reaction distillation column is 2.5MPa, the tower top temperature is -40°C, the reflux ratio is 10:1, and the number of theoretical plates is 80; the silicon tetrachloride / catalyst separation column is an atmospheric distillation column, the column The top temperature is 70°C, the reflux ratio is 3:1, and the number of theoretical plates is 50.
[0071] The silane content in the product prepared by the process of the present invention is 95.6%.
Embodiment 2
[0073] A mixed liquid catalyst of tri-n-hexylamine and N,N-dimethylaniline is used as a trichlorosilane disproportionation reaction catalyst, wherein the n-dodecylamine liquid catalyst mole fraction in the mixed liquid catalyst accounts for 60%, and the catalyst dosage is trichlorohydrogen 10% of the total mass of silicon.
[0074] The operating pressure of the disproportionation reaction distillation tower is 3MPA, the top temperature is -30°C, the reflux ratio is 15:1, and the number of theoretical plates is 80; the top temperature of the silicon tetrachloride / catalyst separation tower is 80°C, the reflux ratio The ratio is 5:1, and the number of theoretical plates is 50.
[0075] The silane content in the product prepared by the process of the present invention is 96%.
Embodiment 3
[0077] A mixed liquid catalyst of tri-n-heptylamine and N,N-di-n-butylaniline is used as a trichlorosilane disproportionation reaction catalyst, wherein the n-dodecylamine liquid catalyst mole fraction accounts for 40% in the mixed liquid catalyst, and the catalyst consumption is three 15% of the total mass of hydrogen chloride silicon.
[0078] The operating pressure of the disproportionation reaction distillation tower is 3.5MPa, the top temperature is -15°C, the reflux ratio is 20:1, and the number of theoretical plates is 80; the top temperature of the silicon tetrachloride / catalyst separation tower is 85°C, and the reflux The ratio is 8:1, and the number of theoretical plates is 50.
[0079] The silane content in the product prepared by the process of the present invention is 97%.
PUM
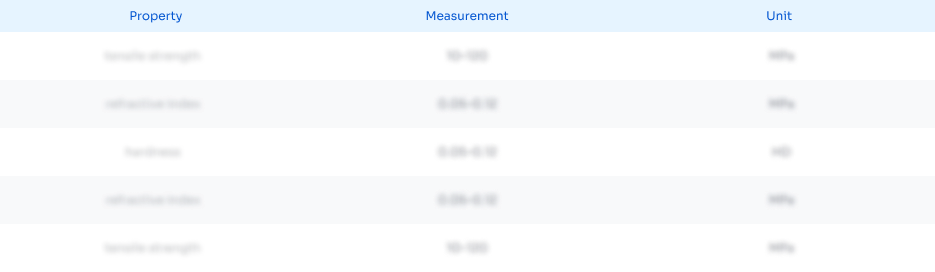
Abstract
Description
Claims
Application Information

- R&D Engineer
- R&D Manager
- IP Professional
- Industry Leading Data Capabilities
- Powerful AI technology
- Patent DNA Extraction
Browse by: Latest US Patents, China's latest patents, Technical Efficacy Thesaurus, Application Domain, Technology Topic, Popular Technical Reports.
© 2024 PatSnap. All rights reserved.Legal|Privacy policy|Modern Slavery Act Transparency Statement|Sitemap|About US| Contact US: help@patsnap.com