Capillary tube throttling dynamic pressure and static pressure mixed bearing used for heavy roll grinder grinding spindle
A roll grinder and hybrid bearing technology, which is applied to the parts of grinding machine tools, grinding/polishing equipment, metal processing equipment, etc. And other issues
- Summary
- Abstract
- Description
- Claims
- Application Information
AI Technical Summary
Problems solved by technology
Method used
Image
Examples
Embodiment Construction
[0027] The technical solutions of the present invention will be further described below in conjunction with the drawings and embodiments.
[0028] Such as Figure 1 to Figure 4 As shown, the structure of the capillary section hydrostatic hybrid bearing used on the main shaft of the grinding wheel of the heavy-duty roll grinder according to the present invention is that an upper static pressure chamber 1, a front static pressure chamber 2, and a lower static pressure chamber 3 are arranged on the bearing cavity wall , the left rear static pressure chamber 8 and the right rear static pressure chamber 9, the arc-shaped shallow chamber 4, the dynamic pressure chamber 5, three axial oil return grooves 6, and the oil inlet hole 7; the upper static pressure chamber 1 and the lower The static pressure chamber 3 is a pair of opposed oil chambers, and the centers of the two oil chambers are located on the vertical line a of the bearing; the center of the front static pressure chamber 2 ...
PUM
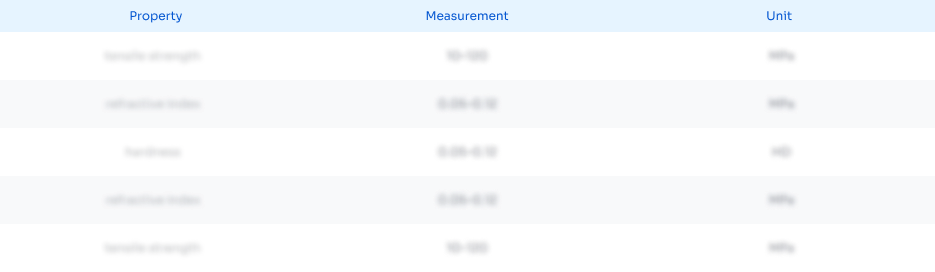
Abstract
Description
Claims
Application Information

- Generate Ideas
- Intellectual Property
- Life Sciences
- Materials
- Tech Scout
- Unparalleled Data Quality
- Higher Quality Content
- 60% Fewer Hallucinations
Browse by: Latest US Patents, China's latest patents, Technical Efficacy Thesaurus, Application Domain, Technology Topic, Popular Technical Reports.
© 2025 PatSnap. All rights reserved.Legal|Privacy policy|Modern Slavery Act Transparency Statement|Sitemap|About US| Contact US: help@patsnap.com