Method for optimizing zinc-hydrometallurgy hot acid leaching process by pressure leaching
A technology for hot acid leaching and hydrometallurgy zinc, applied in the field of zinc hydrometallurgy, can solve the problems of large amount of jarosite slag, unstable properties of jarosite slag, long process flow, etc. Environmental protection and social benefits, the effect of reducing the amount of iron slag
- Summary
- Abstract
- Description
- Claims
- Application Information
AI Technical Summary
Problems solved by technology
Method used
Image
Examples
Embodiment 1
[0023] Add 50g zinc sulfide concentrate (grain size-50um accounts for 96%, zinc: 53.04%, iron 5.70%, sulfur 29.27%) and 750ml hot acid leaching solution (Zn116g / L, H 2 SO 4 40g / L, Fe11.5g / L), add lignosulfonate 0.4%, heat to 130°C, feed oxygen, the oxygen partial pressure is 0.6MPa, control the oxidation leaching reaction temperature 130-140°C, react for 3 hours, in During the pressure leaching process, no other additives and catalysts are needed except for oxygen and lignosulfonate. After the reaction, the slurry is filtered to obtain 680ml leachate (containing Zn: 149g / l, Fe: 2.69g / l, H 2 SO 4 : 10.2g / L) and 37.4g leaching slag (zinc: 2.14%, Fe19.25%, sulfur 35.7%). 96.98% of the zinc is leached during the pressure oxidation leaching process.
Embodiment 2
[0025] Add 50g zinc sulfide concentrate (grain size-50um accounts for 96%, zinc: 53.04%, iron 5.70%, sulfur 29.27%) and 700ml hot acid leaching solution (Zn116g / L, H 2 SO 4 40g / L, Fe11.5g / L), add lignosulfonate 0.4%, heat to 130°C, feed oxygen, the oxygen partial pressure is 0.6MPa, control the oxidation leaching reaction temperature 130-140°C, react for 3 hours, in During the pressure leaching process, no other additives and catalysts need to be added except oxygen and lignosulfonate. After the reaction, the slurry is filtered to obtain 625ml leachate (containing Zn: 154g / l, Fe: 1.54g / l, H 2 SO 4 : 8.9g / L) and 36.1g leaching slag (zinc: 1.92%, Fe22.56%, sulfur 38.4%). 97.39% of the zinc was leached during the pressure oxidation leaching process.
Embodiment 3
[0027] Add 50g zinc sulfide concentrate (grain size-50um accounts for 96%, zinc: 53.04%, iron 5.70%, sulfur 29.27%) and 720ml hot acid leaching solution (Zn116g / L, H 2 SO 4 40g / L, Fe11.5g / L), add lignosulfonate 0.4%, heat to 130°C, feed oxygen, the oxygen partial pressure is 0.6MPa, control the oxidation leaching reaction temperature 130-140°C, react for 3 hours, in During the pressure leaching process, no other additives and catalysts need to be added except oxygen and lignosulfonate. After the reaction, the slurry is filtered to obtain 645ml leachate (containing Zn: 152g / l, Fe: 2.41g / l, H 2 SO 4 : 9.6g / L) and 36.3g leaching slag (zinc: 1.98%, Fe19.35%, sulfur 34.9%). 97.29% of the zinc was leached during the pressure oxidation leaching process.
PUM
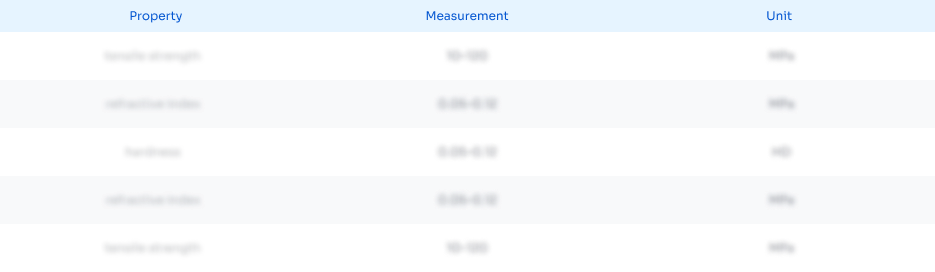
Abstract
Description
Claims
Application Information

- R&D Engineer
- R&D Manager
- IP Professional
- Industry Leading Data Capabilities
- Powerful AI technology
- Patent DNA Extraction
Browse by: Latest US Patents, China's latest patents, Technical Efficacy Thesaurus, Application Domain, Technology Topic, Popular Technical Reports.
© 2024 PatSnap. All rights reserved.Legal|Privacy policy|Modern Slavery Act Transparency Statement|Sitemap|About US| Contact US: help@patsnap.com