Method for preparing weather-resistant cable sheath material
A cable sheath and weather-resistant technology, applied in the direction of insulated cables, cables, circuits, etc., can solve the problems of environmental crack resistance, high and low temperature resistance and weather resistance, internal transmission medium leakage, long service life of rubber, etc., to achieve easy Improve cracking, eliminate internal stress, and have strong environmental cracking resistance
- Summary
- Abstract
- Description
- Claims
- Application Information
AI Technical Summary
Problems solved by technology
Method used
Image
Examples
preparation example Construction
[0014] refer to figure 1 , a preparation method of a weather-resistant cable sheath material, comprising the steps of:
[0015] S1. Weigh 60-75% PVC resin, 3-15% linear low-density PE resin and 15-25% ethylene-vinyl acetate copolymer to obtain the main material by weight percentage, and place the prepared main material in a single screw Blend in the extruder and granulate to get the base resin, turn on the internal mixer and preheat to 40-60°C, then add the above base resin for banburying, the mixing time is 1-3min, and raise the temperature to 80-90°C Tempering for 4-5 minutes;
[0016] S2. Add plasticizer equivalent to 1-3wt% of the main material, 4-8wt% (talcum powder + nano calcium carbonate), 2-3.5wt% stabilizer, 15-20wt% MBS to the prepared material Resin, 0.05-0.1wt% of lubricating additives are mixed evenly, and the weight ratio of talcum powder to nano-calcium carbonate is 1: (1-2.5); among them, plasticizers, fillers, talcum powder and nano-calcium carbonate are ad...
Embodiment 1
[0019] A preparation method for a weather-resistant cable sheath material, comprising the steps of:
[0020] S1. Take 60% PVC resin, 15% linear low-density PE resin and 25% ethylene-vinyl acetate copolymer and mix them evenly to obtain the main material by weight percentage, and place the prepared main material in a single-screw extruder for blending, Pellet to obtain the base resin, turn on the internal mixer and preheat to 60°C, then add the above base resin for banburying, the mixing time is 1min, and banburying for 4min when the temperature rises to 80°C;
[0021] S2, add the plasticizer equivalent to main material 2.8wt% in the prepared material, 7wt% (talcum powder+nanometer calcium carbonate), the stabilizer of 2.3wt%, the MBS resin of 15wt%, the lubricant of 0.85wt% The additives are mixed evenly, and the weight ratio of talcum powder to nano-calcium carbonate is 1:1.7; the plasticizer, filler, talc powder and nano-calcium carbonate are added alternately in stages duri...
Embodiment 2
[0024] A preparation method for a weather-resistant cable sheath material, comprising the steps of:
[0025] S1. Weigh 75% PVC resin, 5% linear low-density PE resin and 20% ethylene-vinyl acetate copolymer and mix uniformly to obtain the main material by weight percentage, and place the prepared main material in a single-screw extruder for blending, Granulate to obtain the base resin, turn on the internal mixer and preheat to 40°C, then add the above base resin for banburying, the banburying time is 2.5min, when the temperature rises to 85°C, banburying 5min;
[0026] S2, add the plasticizer equivalent to main material 2.5wt% in the prepared material, 7wt% (talcum powder+nanometer calcium carbonate), the stabilizer of 2wt%, the MBS resin of 20wt%, the lubricating aid of 0.067wt% The agent is mixed evenly, and the weight ratio of talcum powder and nano-calcium carbonate is 1:2.5; the plasticizer, filler, talcum powder and nano-calcium carbonate are added alternately in stages d...
PUM
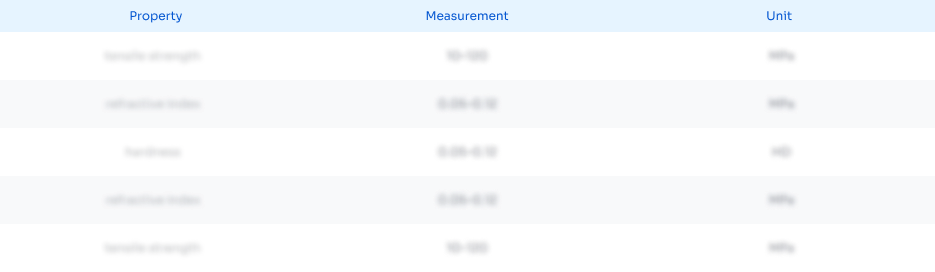
Abstract
Description
Claims
Application Information

- R&D
- Intellectual Property
- Life Sciences
- Materials
- Tech Scout
- Unparalleled Data Quality
- Higher Quality Content
- 60% Fewer Hallucinations
Browse by: Latest US Patents, China's latest patents, Technical Efficacy Thesaurus, Application Domain, Technology Topic, Popular Technical Reports.
© 2025 PatSnap. All rights reserved.Legal|Privacy policy|Modern Slavery Act Transparency Statement|Sitemap|About US| Contact US: help@patsnap.com