Tin-indium alloy coated copper wire and production method thereof
A technology of tin-indium alloy and production method, which is applied to the production of plated copper wire and the field of tin-indium alloy plated copper wire, can solve the problems of uneven thickness of the coating, environmental pollution, unsmooth appearance of the coating, etc. Uniformity, improved cleaning effect
- Summary
- Abstract
- Description
- Claims
- Application Information
AI Technical Summary
Problems solved by technology
Method used
Image
Examples
Embodiment 1
[0029] The production method of the tin-indium alloy plated copper wire of the present embodiment comprises the following steps:
[0030] A. Make copper rods. The copper rod is made of oxygen-free copper with a copper content of more than 99.98%.
[0031] B. Drawing the above-mentioned copper rod through a wire drawing machine to obtain an oxygen-free copper wire core; the cross-section of the wire core and the finally prepared alloy-coated copper wire is approximately circular.
[0032] In this step, the area reduction rate of the wire drawing die is 13% to 17%, the line speed is 2000 m / min to 2500 m / min, the wire drawing die adopts a polycrystalline diamond die, and its compression angle is 18 ○ ±2 ○ , and the sizing length is 40% ± 10%; in the present embodiment, the lubricating liquid formulation adopted in the drawing process is as follows: 15% modified castor oil, 15% modified sunflower oil, 10% sodium petroleum sulfonate, isothiazole Linone 1‰, triethanolamine 3%, be...
Embodiment 2
[0048] In this example, the lubricating fluid formula used in the drawing process is as follows: 18% modified castor oil, 10% modified sunflower oil, 8% sodium petroleum sulfonate, 1‰ isothiazolinone, 3% triethanolamine, benzene Paratriazole 0.4%, benzene 3%, caustic soda 7%, and the balance is refined machinery oil. All the other production techniques are with embodiment one.
[0049] The tin-indium alloy coated copper wire produced by the present invention reaches the following indicators after testing:
[0050] Comparison table of physical and chemical performance parameters
[0051] Test items Detection method Silver plated soft round copper wire Tinned soft round copper wire Product of the present invention Elongation % GB / T4909.3-2009 20 15 20 ResistivityΩmm2 / m GB / T3048.2-2007 0.017241 0.01770 0.01732 Plating Continuity GB / T4909.9-2009 sodium polysulfide method or ammonium persulfate method Better than required meet the ...
PUM
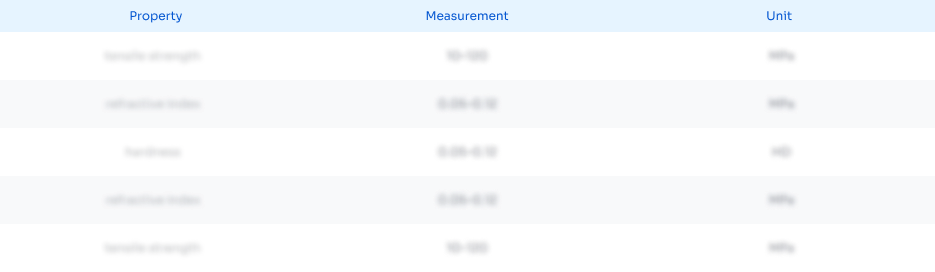
Abstract
Description
Claims
Application Information

- R&D Engineer
- R&D Manager
- IP Professional
- Industry Leading Data Capabilities
- Powerful AI technology
- Patent DNA Extraction
Browse by: Latest US Patents, China's latest patents, Technical Efficacy Thesaurus, Application Domain, Technology Topic, Popular Technical Reports.
© 2024 PatSnap. All rights reserved.Legal|Privacy policy|Modern Slavery Act Transparency Statement|Sitemap|About US| Contact US: help@patsnap.com