Stirring head for friction stir welding used for welding parts with different thicknesses and welding method
A friction stir welding and stirring head technology, which is applied in welding/welding/cutting items, welding equipment, non-electric welding equipment, etc., can solve the problems of increasing welding difficulty and cost, large impact on joint performance, and high operation control requirements. Guarantee the quality of welded joints, simplify the requirements of equipment and welding methods, and simplify the effect of the welding process
- Summary
- Abstract
- Description
- Claims
- Application Information
AI Technical Summary
Problems solved by technology
Method used
Image
Examples
Embodiment 1
[0023] Welding 6082 aluminum alloys with different thicknesses, the base metal thicknesses are 5mm and 7mm respectively.
[0024] The diameter of the shaft shoulder of the processing stirring head is Φ12mm, the angle of the cutting auxiliary shaft shoulder is 45°, and the height is 10mm.
[0025] Welding process: place the stirring head on the welding equipment, and rotate it at 500-1500 rpm, the direction of rotation is counterclockwise, after the shaft shoulder touches the upper surface of the base metal of the thin plate, continue to rotate and stay on the workpiece for 5-10 seconds After that, it is then welded along the seam. The test results show that there is no defect inside the joint, and the fracture positions of the tensile test pieces are all in the heat-affected zone of the friction stir welded joint of the 5mm base metal.
Embodiment 2
[0027] Welding 2024 aluminum alloy with different thickness, the base metal thickness is 2mm and 4mm respectively;
[0028] The diameter of the shaft shoulder of the processing stirring head is Φ10mm, the angle of the cutting auxiliary shaft shoulder is 8°, and the height is 14mm.
[0029] Welding process: place the stirring head on the welding equipment, and rotate it at 800-2000 rpm, the direction of rotation is clockwise, after the shaft shoulder touches the upper surface of the base metal of the thin plate, it will continue to rotate and stay on the workpiece for 3-8 seconds After that, it is then welded along the seam. The test results show that there is no defect inside the surface joint, and the fracture positions of the tensile test pieces are all in the friction stir welded joint on the 2mm base metal side.
Embodiment 3
[0031] Welding 2024 and 6082 aluminum alloys with different thicknesses, the thickness of 2024 aluminum alloy is 4mm, and the thickness of 6082 aluminum alloy is 4.5mm, 5mm, 5.5mm and 6mm respectively.
[0032] The diameter of the shaft shoulder of the processing stirring head is Φ15mm, the angle of the cutting auxiliary shaft shoulder is 70°, and the height is 20mm.
[0033] Welding process: place the stirring head on the welding equipment and rotate it at 600-1000 rpm, the direction of rotation is counterclockwise, after the shaft shoulder touches the upper surface of the 2024 aluminum alloy base material, it will continue to rotate and stay on the workpiece for 5- After 10 seconds, then weld along the seam. The test results show that there are no defects inside the surface joint, and the fracture position of the tensile test piece is at the edge of the friction stir welded joint on the 6082 side. The results are as follows image 3 shown.
PUM
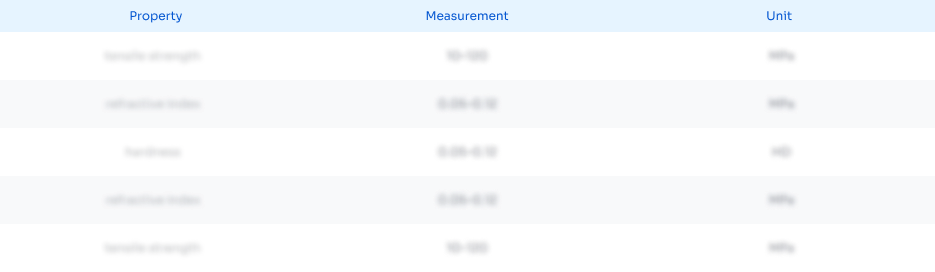
Abstract
Description
Claims
Application Information

- R&D
- Intellectual Property
- Life Sciences
- Materials
- Tech Scout
- Unparalleled Data Quality
- Higher Quality Content
- 60% Fewer Hallucinations
Browse by: Latest US Patents, China's latest patents, Technical Efficacy Thesaurus, Application Domain, Technology Topic, Popular Technical Reports.
© 2025 PatSnap. All rights reserved.Legal|Privacy policy|Modern Slavery Act Transparency Statement|Sitemap|About US| Contact US: help@patsnap.com