Polycrystalline diamond catalyst and thermal treatment process thereof
A polycrystalline diamond and catalyst technology, applied in the field of artificial diamond, can solve the problems of inability to form polycrystalline diamond structure, low strength, and large magnetic properties of single crystal diamond, and achieve the effect of less impurities, high yield per unit area, and rough surface
- Summary
- Abstract
- Description
- Claims
- Application Information
AI Technical Summary
Problems solved by technology
Method used
Examples
Embodiment 1
[0012] The weight percentage of the chemical composition of the polycrystalline diamond catalyst is: 3% cobalt, 34% iron, 27% manganese, 20% nickel, 13% silicon and 3% carbon.
[0013] The heat treatment process for the above polycrystalline diamond catalyst includes the following steps:
[0014] 1). Divide the aforementioned catalyst into three particle sizes: 80 / 100, 200 / 250 and 300 / 400;
[0015] 2). Mix the catalysts with three particle sizes in step 1) in a ratio of 2:3:5;
[0016] 3) Put the mixed catalyst in step 2) into the muffle furnace in a stainless steel box and bake at 580°C for 28 minutes to obtain a new type of catalyst with irregular particles.
Embodiment 2
[0018] Cobalt 4%, iron 31%, manganese 27%, nickel 22%, silicon 13% and carbon 3%.
[0019] The heat treatment process for the above polycrystalline diamond catalyst includes the following steps:
[0020] 1). Divide the aforementioned catalyst into three particle sizes: 80 / 100, 200 / 250 and 300 / 400;
[0021] 2). Mix the catalysts with three particle sizes in step 1) in a ratio of 2:3:5;
[0022] 3) Put the mixed catalyst in step 2) into the muffle furnace in a stainless steel box and bake at 700°C for 14 minutes to obtain a new type of catalyst with irregular shaped particles.
Embodiment 3
[0024] Cobalt 3.5%, iron 30%, manganese 30%, nickel 19%, silicon 14% and carbon 3.5%.
[0025] The heat treatment process for the above polycrystalline diamond catalyst includes the following steps:
[0026] 1). Divide the aforementioned catalyst into three particle sizes: 80 / 100, 200 / 250 and 300 / 400;
[0027] 2). Mix the catalysts with three particle sizes in step 1) in a ratio of 2:3:5;
[0028] 3) Put the mixed catalyst in step 2) into the muffle furnace in a stainless steel box and bake at 650°C for 22 minutes to obtain a new type of catalyst with irregularly shaped particles.
PUM
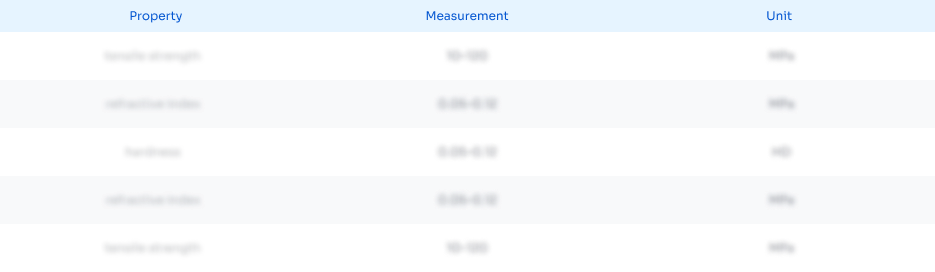
Abstract
Description
Claims
Application Information

- R&D Engineer
- R&D Manager
- IP Professional
- Industry Leading Data Capabilities
- Powerful AI technology
- Patent DNA Extraction
Browse by: Latest US Patents, China's latest patents, Technical Efficacy Thesaurus, Application Domain, Technology Topic, Popular Technical Reports.
© 2024 PatSnap. All rights reserved.Legal|Privacy policy|Modern Slavery Act Transparency Statement|Sitemap|About US| Contact US: help@patsnap.com