A New High Efficiency Smokeless Backburning Boiler
A high-efficiency and new technology, applied in the field of hot water boilers, can solve the problems of poor anti-burning effect, unreasonable setting of inclination angle and size of coal leakage gap, unreasonable setting of high and low positions, etc.
- Summary
- Abstract
- Description
- Claims
- Application Information
AI Technical Summary
Problems solved by technology
Method used
Image
Examples
Embodiment Construction
[0017] The accompanying drawings of the description show an embodiment of the present invention. The reverse combustion boiler includes a cylindrical furnace body, a water bag interlayer of the furnace body, a coal feeding furnace door, a water pipe reverse combustion furnace grate, a combustion chamber, an ash chamber, a fire passage, a flue gas residual hot water bag and a smoke exhaust port. The water pipe anti-burning furnace grate 6 is located in the middle part of the furnace body. The combustion chamber includes a dry distillation combustion chamber 5 above the water pipe reverse combustion furnace grate and a reverse combustion combustion chamber 7 under the water pipe reverse combustion furnace grate. The chamber 7 is provided with an operating furnace door 8 on the front side of the furnace body. The rear side of the combustion chamber is provided with a burner port 13 connected to the exhaust pipe of the residual hot water bag of the flue gas, and the exhaust pipe ...
PUM
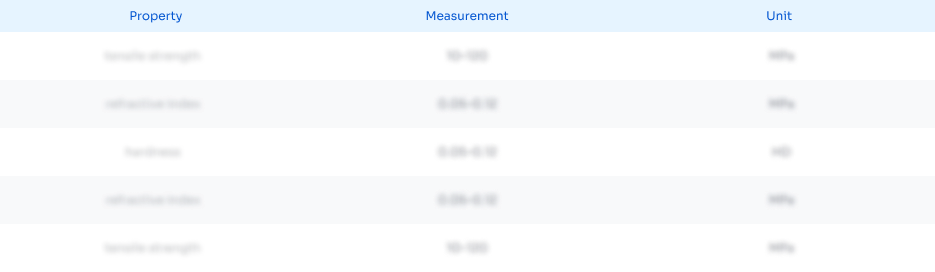
Abstract
Description
Claims
Application Information

- R&D
- Intellectual Property
- Life Sciences
- Materials
- Tech Scout
- Unparalleled Data Quality
- Higher Quality Content
- 60% Fewer Hallucinations
Browse by: Latest US Patents, China's latest patents, Technical Efficacy Thesaurus, Application Domain, Technology Topic, Popular Technical Reports.
© 2025 PatSnap. All rights reserved.Legal|Privacy policy|Modern Slavery Act Transparency Statement|Sitemap|About US| Contact US: help@patsnap.com