Oxygen-rich blowing technology for producing coarse lead and matte from lead matte in top-blowing furnace
A lead matte and top-blowing furnace technology, applied in furnaces, electric furnaces, rotary drum furnaces, etc., to achieve the effects of low operating costs, reduced emissions, and high smelting recovery
- Summary
- Abstract
- Description
- Claims
- Application Information
AI Technical Summary
Problems solved by technology
Method used
Image
Examples
Embodiment 1
[0014] Example 1: A 300mm deep lead smelting FeO-SiO is left in a top-blowing furnace with an inner diameter of 5m 2 -CaO ternary slag starting pool, slag FeO / SiO 2 The weight ratio is 0.9, CaO / SiO 2 The weight ratio is 0.8, and the silicic acidity is 1.24; the lead matte with the mixture of lead sulfide and copper sulfide as the main component is continuously put into the top-blowing furnace at a rate of 50t / h, and the blowing temperature is controlled between 1200 and 1250 °C . According to the sulfur content of the lead matte, the sulfur in the lead sulfide in the lead matte is completely oxidized to SO 2 According to the chemical reaction requirements, calculate the amount of oxygen that needs to be added per unit time, add oxygen-enriched air from the spray gun, and carry out continuous oxidation and blowing for 6 hours. Through oxygen-enriched air oxidation blowing, the lead sulfide in the lead matte is oxidized to lead oxide, and at the same time, part of the lead ...
Embodiment 2
[0015] Example 2: In a top-blowing furnace with an inner diameter of 5m, there is a 350mm deep lead smelting FeO-SiO 2 -CaO ternary slag starting pool, slag FeO / SiO 2 The weight ratio is 1.0, CaO / SiO 2 The weight ratio is 0.6, and the silicic acidity is 1.35; the lead matte with the mixture of lead sulfide and copper sulfide as the main component is continuously put into the top-blowing furnace at a rate of 55t / h, and the blowing temperature is controlled between 1180 and 1260 °C . According to the sulfur content of the lead matte, the sulfur in the lead sulfide in the lead matte is completely oxidized to SO 2 According to the chemical reaction requirements, calculate the amount of oxygen that needs to be added per unit time, add oxygen-enriched air from the spray gun, and carry out continuous oxidation and blowing for 5.5 hours. Through oxygen-enriched air oxidation blowing, the lead sulfide in the lead matte is oxidized to lead oxide, and at the same time, part of the l...
Embodiment 3
[0016] Example 3: A 300mm deep lead smelting FeO-SiO is left in a top-blowing furnace with an inner diameter of 5m 2 -CaO ternary slag starting pool, slag FeO / SiO 2 The weight ratio is 1.2, CaO / SiO 2 The weight ratio is 0.7, and the silicic acidity is 1.14; the lead matte with the mixture of lead sulfide and copper sulfide as the main component is continuously put into the top-blowing furnace at a speed of 60t / h, and the blowing temperature is controlled between 1200 and 1250°C . According to the sulfur content of the lead matte, the sulfur in the lead sulfide in the lead matte is completely oxidized to SO 2 According to the chemical reaction requirements, calculate the amount of oxygen that needs to be added per unit time, add oxygen-enriched air from the spray gun, and carry out continuous oxidation and blowing for 5.5 hours. Through oxygen-enriched air oxidation blowing, the lead sulfide in the lead matte is oxidized to lead oxide, and at the same time, part of the lea...
PUM
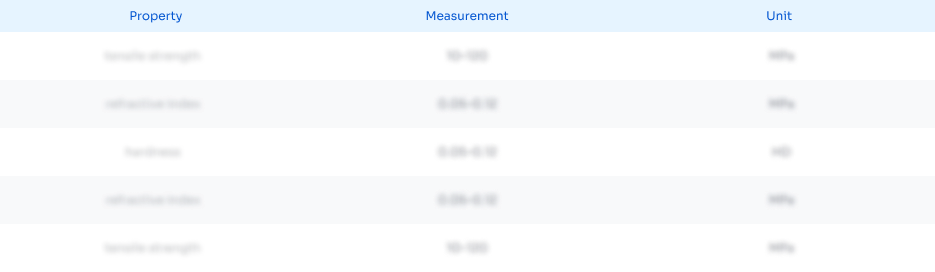
Abstract
Description
Claims
Application Information

- R&D
- Intellectual Property
- Life Sciences
- Materials
- Tech Scout
- Unparalleled Data Quality
- Higher Quality Content
- 60% Fewer Hallucinations
Browse by: Latest US Patents, China's latest patents, Technical Efficacy Thesaurus, Application Domain, Technology Topic, Popular Technical Reports.
© 2025 PatSnap. All rights reserved.Legal|Privacy policy|Modern Slavery Act Transparency Statement|Sitemap|About US| Contact US: help@patsnap.com