Method for smelting FeV80 by using vanadium-aluminum residual alloy
A vanadium-aluminum alloy and alloy technology, applied in the field of smelting FeV80 by using vanadium-aluminum residual alloy, can solve the problems of low utilization rate of vanadium-aluminum residual alloy resources, splashing, smelting furnace is easy to be corroded, etc., to improve the on-site operation environment, The effect of reducing TV content and improving kinetic conditions
- Summary
- Abstract
- Description
- Claims
- Application Information
AI Technical Summary
Problems solved by technology
Method used
Image
Examples
Embodiment 1
[0044] (1) 3226kg sheet vanadium, 3548kgAlV55 residual alloy, 940kg iron filings and 161kg lime are mixed to obtain a mixture;
[0045] (2) The mixture obtained in step (1) is transferred to a straight cylinder furnace (furnace lining is magnesia) for arc-starting smelting, and the smelting time is 88min; the furnace body is rotated, and then 160kg of refining agent (by weight ratio) is added using the blowing system It is obtained by mixing aluminum powder and lime at 1:1.5) for refining. During the refining process, electrode heating is used to maintain the system temperature at 1900 ° C. The refining time is 28 minutes. Then the straight cylinder furnace is transferred to the cooling zone for cooling. The cooling time is 20 hours, and then Ferrovanadium alloy cake A1 and ferrovanadium smelting slag B1 are obtained by separation.
Embodiment 2
[0047] (1) 3230kg sheet vanadium, 4199kgAlV55 residual alloy, 1030kg iron filings and 226kg lime are mixed to obtain a mixture;
[0048](2) Transfer the mixture obtained in step (1) to a straight cylinder furnace (furnace lining is magnesia) for arc-starting smelting, and the smelting time is 96min; the furnace body is rotated, and then 180% refining agent (by weight ratio) is added using the blowing system It is obtained by mixing aluminum powder and lime at 1:1.3) for refining. During the refining process, electrode heating is used to maintain the system temperature at 2000 ° C. The refining time is 32 minutes. Then the straight cylinder furnace is transferred to the cooling zone for cooling. The cooling time is 24 hours, and then Ferrovanadium alloy cake A2 and ferrovanadium smelting slag B2 are obtained by separation.
Embodiment 3
[0050] (1) 3235kg sheet vanadium, 4205kgAlV65 residual alloy, 1136kg iron filings and 324kg lime are mixed to obtain a mixture;
[0051] (2) The mixture obtained in step (1) is transferred to the straight tube furnace (furnace lining is magnesia) for arc-starting smelting, and the smelting time is 100min; the body of the furnace is rotated, and then 170kg of refining agent (by weight ratio) is added by the blowing system It is obtained by mixing aluminum powder and lime at 1:1.5) for refining. During the refining process, electrode heating is used to maintain the system temperature at 1950°C. The refining time is 35 minutes. Then the straight cylinder furnace is transferred to the cooling zone for cooling. The cooling time is 24 hours, and then Ferrovanadium alloy cake A3 and ferrovanadium smelting slag B3 are obtained by separation.
PUM
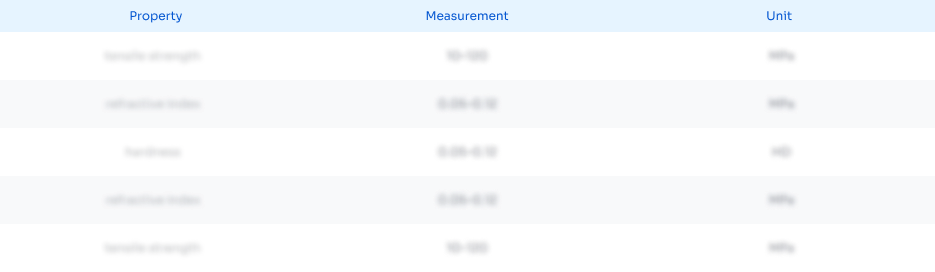
Abstract
Description
Claims
Application Information

- R&D
- Intellectual Property
- Life Sciences
- Materials
- Tech Scout
- Unparalleled Data Quality
- Higher Quality Content
- 60% Fewer Hallucinations
Browse by: Latest US Patents, China's latest patents, Technical Efficacy Thesaurus, Application Domain, Technology Topic, Popular Technical Reports.
© 2025 PatSnap. All rights reserved.Legal|Privacy policy|Modern Slavery Act Transparency Statement|Sitemap|About US| Contact US: help@patsnap.com