Steatite ceramic compound grinding aid and preparation method thereof
A technology of talc porcelain and grinding aid, applied in chemical instruments and methods, other chemical processes, etc., can solve the problems of increasing the viscosity of talc porcelain mud, reducing grinding efficiency, etc., achieving good grinding aid performance, shortening grinding time, good The effect of grinding aid
- Summary
- Abstract
- Description
- Claims
- Application Information
AI Technical Summary
Problems solved by technology
Method used
Examples
Embodiment 1
[0014] Example 1 The talc-porcelain composite grinding aid consists of the following raw materials in parts by mass:
[0015] Vinyl bis stearamide 15 parts
[0016] Polyethylene glycol fatty acid ester 15 parts
[0017] Sodium metasilicate 38 parts
[0018] Sodium hexametaphosphate 22 parts
[0019] After the above-mentioned raw materials are accurately weighed, they are fully stirred in a mixer to obtain a powdery mixture with no agglomerated particles and uniform color, which is packed into a sealed packaging bag to obtain the finished product of the talc-porcelain composite grinding aid.
[0020] When in use, take out the talc-porcelain composite grinding aid from the sealed packaging bag, add 3.5 kilograms of additives per ton of dry base ceramic raw materials, and add it into the ball mill after accurate weighing.
[0021] Compared with the blank sample without any additives, after adding 0.35% talc porcelain composite grinding aid, the ball milling time was shorten...
Embodiment 2
[0022] Example 2 The talc-porcelain composite grinding aid consists of the following raw materials in parts by mass:
[0023] Triethylhexyl phosphate 13
[0024] Polyethylene glycol 16
[0025] Sodium tripolyphosphate 30
[0026] Sodium metasilicate 25
[0027] Triethanolamine 16
[0028] First add 400 parts of deionized water to the container, then add accurately weighed triethylhexyl phosphate, polyethylene glycol, sodium tripolyphosphate, sodium metasilicate in sequence, and stir in a water bath at 80°C for 3 hours , then add triethanolamine, continue to stir for 0.5 hours, and finally pass the obtained liquid through a 250-mesh vibrating sieve to remove solid impurities therein, and obtain a finished product of talc-porcelain composite grinding aid with a solid content of 20%.
[0029] When in use, add 4.5 kilograms of additives per ton of dry base ceramic raw material, accurately weigh and add to the ball mill.
[0030] Compared with the blank sample without any ...
Embodiment 3
[0031] Example 3 : The talc porcelain composite grinding aid is made up of the following raw materials in parts by mass:
[0032] Polyethyleneimine 22
[0033] Polyethylene glycol 18
[0034] Sodium dodecylbenzenesulfonate 15
[0035] Sodium hexametaphosphate 30
[0036] Triisopropanolamine 15
[0037] First add 500 parts of deionized water to the container, then add accurately weighed polyethyleneimine, polyethylene glycol, sodium dodecylbenzenesulfonate, and sodium hexametaphosphate in sequence, and stir in a water bath at 60°C for 4 After one hour, add triisopropanolamine, continue to stir for 1 hour, and finally pass the obtained liquid through a 250-mesh vibrating sieve to remove solid impurities therein, and obtain a finished product of talc porcelain composite grinding aid with a solid content of 16.7%.
[0038] When in use, add 5 kg of additives per ton of dry base ceramic raw material, accurately weigh and add to the ball mill.
[0039] Compared with the blank ...
PUM
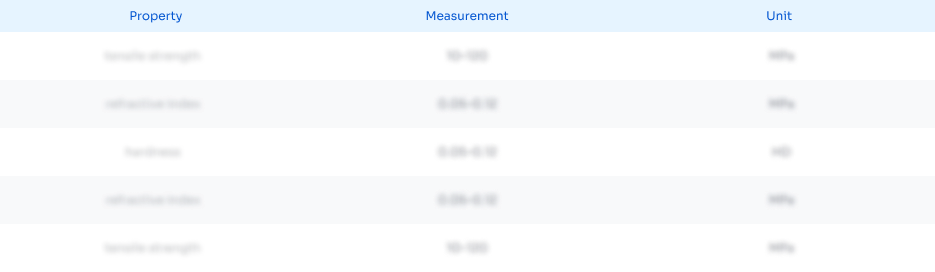
Abstract
Description
Claims
Application Information

- R&D
- Intellectual Property
- Life Sciences
- Materials
- Tech Scout
- Unparalleled Data Quality
- Higher Quality Content
- 60% Fewer Hallucinations
Browse by: Latest US Patents, China's latest patents, Technical Efficacy Thesaurus, Application Domain, Technology Topic, Popular Technical Reports.
© 2025 PatSnap. All rights reserved.Legal|Privacy policy|Modern Slavery Act Transparency Statement|Sitemap|About US| Contact US: help@patsnap.com