Preparation method of high-temperature resistance multilayer precoated sand
A technology of coated sand and high temperature resistance, applied in chemical instruments and methods, drilling compositions, etc., can solve the problems of easy falling off, affecting the comprehensive development effect of oil and gas fields, poor application effect, etc., and achieve the effect of satisfying one-time sand control.
- Summary
- Abstract
- Description
- Claims
- Application Information
AI Technical Summary
Problems solved by technology
Method used
Image
Examples
Embodiment 1
[0027] The preparation method of the high temperature resistant multi-layer film is carried out as follows:
[0028] a. Heat the sieved quartz sand or ceramsite with a particle size of 0.3-0.6mm to 150°C in a high-temperature furnace and put it into the first-stage sand mixer. Methylenetetramine=100:8:10 parts by weight, first spray into the coating material, after stirring for 20s, then add hexamethylenetetramine, and continue stirring for 90s to obtain pre-cured coated quartz sand or ceramsite; The coating material is a modified phenolic resin prepared by reacting 3 parts by weight of organosilicon, 8 parts by weight of coal tar and 95 parts by weight of thermoplastic phenolic resin at a temperature of 75° C. for 5 hours;
[0029] b. Put the pre-cured coated quartz sand or ceramsite in step a into the secondary sand mixer and heat it to 180°C, and stir according to the pre-cured coated quartz sand or ceramsite: unsaturated resin: silicone: six times Methyltetramine=100:9:2:...
Embodiment 2
[0032] The preparation method of the high temperature resistant multi-layer film is carried out as follows:
[0033] a. Heat the sieved quartz sand or ceramsite with a particle size of 0.3-0.6mm to 180°C in a high-temperature furnace and put it into the first-stage sand mixer. Methylenetetramine=100:6:12 parts by weight, first spray into the coating material, stir for 10s, then add hexamethylenetetramine, and continue stirring for 240s to obtain pre-cured coated quartz sand or ceramsite; The coating material is a modified phenolic resin prepared by reacting 1 weight part of organic silicon, 12 weight parts of coal tar and 85 weight parts of thermoplastic phenolic resin at a temperature of 85° C. for 4 hours;
[0034] b. Put the pre-cured coated quartz sand or ceramsite in step a into the secondary sand mixer and heat it to 150°C, and stir according to the pre-cured coated quartz sand or ceramsite: unsaturated resin: silicone: six times Methyltetramine=100:7:3:2 parts by weigh...
Embodiment 3
[0037] The preparation method of the high temperature resistant multi-layer film is carried out as follows:
[0038] a. Heat the sieved quartz sand or ceramsite with a particle size of 0.3-0.6mm to 160°C in a high-temperature furnace and put it into the first-stage sand mixer. Methylenetetramine=100:7:11 parts by weight, first spray into the coating material, stir for 15s, then add hexamethylenetetramine, and continue stirring for 160s to obtain pre-cured coated quartz sand or ceramsite; The coating material is a modified phenolic resin prepared by reacting 2 parts by weight of organosilicon, 10 parts by weight of coal tar and 90 parts by weight of thermoplastic phenolic resin at a temperature of 80° C. for 4.5 hours;
[0039]b. Put the pre-cured coated quartz sand or ceramsite in step a into the secondary sand mixer and heat it to 170°C, and stir according to the pre-cured coated quartz sand or ceramsite: unsaturated resin: silicone: six times Methyltetramine=100:8:2.5:3 par...
PUM
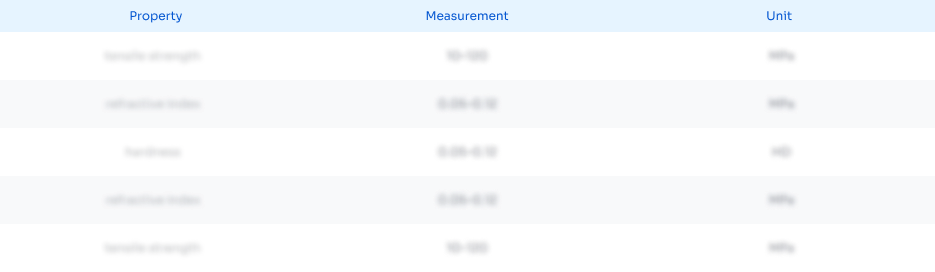
Abstract
Description
Claims
Application Information

- R&D
- Intellectual Property
- Life Sciences
- Materials
- Tech Scout
- Unparalleled Data Quality
- Higher Quality Content
- 60% Fewer Hallucinations
Browse by: Latest US Patents, China's latest patents, Technical Efficacy Thesaurus, Application Domain, Technology Topic, Popular Technical Reports.
© 2025 PatSnap. All rights reserved.Legal|Privacy policy|Modern Slavery Act Transparency Statement|Sitemap|About US| Contact US: help@patsnap.com