Production method of breathable leather
A production method and technology of air-permeable leather, applied in the direction of chemical instruments and methods, layered products, textiles and papermaking, etc., can solve the problems of difficult to achieve hydrolysis resistance, poor hydrolysis resistance, high content of dimethylformamide, etc., to avoid Poor environmental pollution and hydrolysis resistance, lower production cost, and increased perspiration function
- Summary
- Abstract
- Description
- Claims
- Application Information
AI Technical Summary
Problems solved by technology
Method used
Image
Examples
Embodiment 1
[0023] see figure 1 , The production method of air-permeable leather in this embodiment includes the following steps in sequence.
[0024] ① The batching room prepares the slurry according to the technical formula sheet and the order quantity of 1000 meters. The slurry is composed of polyurethane resin and color chips, and the weight ratio of polyurethane resin and color chips is 100:1.2. Adjust the viscosity of the slurry and mix the slurry The viscosity of the material is adjusted to 1500cps, and the color water refers to the customer's sample. Step?? provides raw materials for step??. The slurry used is simple in composition and scientific in proportion, which can effectively improve the air permeability and hydrolysis resistance of leather, with remarkable effect.
[0025] ②The PU production line selects the required release paper according to the customer's requirements, sets the drying temperature to 100°C, and then coats the release paper, that is, coats the slurry on ...
Embodiment 2
[0032] see figure 1 , The production method of air-permeable leather in this embodiment includes the following steps in sequence.
[0033] ① Prepare the slurry, which is composed of polyurethane resin and color chips, and the weight ratio of polyurethane resin and color chips is 100:1.2, and adjust the viscosity of the slurry to 1500cps.
[0034] ②Put the release paper on the PU production line. The release paper is conveyed at a linear speed of 15.8m / min. First, the release paper is dried at a temperature of 100°C, and then the slurry is coated on the release paper. Then dry at 140°C, cool to 5-8°C, and then wind up at a linear speed of 15.8m / min to obtain a semi-finished product. The surface of the semi-finished product is breathable. , the gas pressure on the front of the semi-finished product is not less than 0.25kg.
[0035] ③ Use a three-plate printing machine to print patterns and gloss on the dry surface of the release paper, and roll it after cooling. The linear spe...
PUM
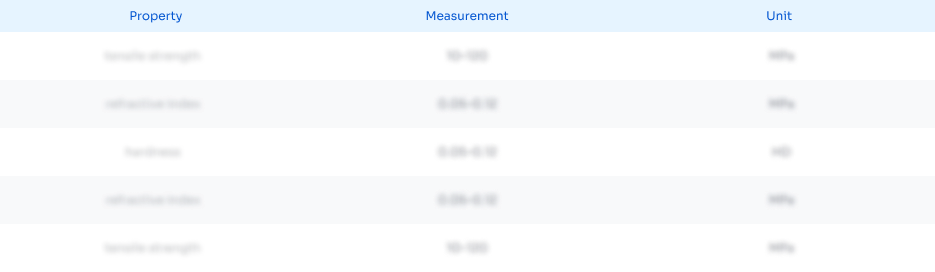
Abstract
Description
Claims
Application Information

- R&D
- Intellectual Property
- Life Sciences
- Materials
- Tech Scout
- Unparalleled Data Quality
- Higher Quality Content
- 60% Fewer Hallucinations
Browse by: Latest US Patents, China's latest patents, Technical Efficacy Thesaurus, Application Domain, Technology Topic, Popular Technical Reports.
© 2025 PatSnap. All rights reserved.Legal|Privacy policy|Modern Slavery Act Transparency Statement|Sitemap|About US| Contact US: help@patsnap.com