Method for sealing air removal and extraction pipe of composite sheath by hydraulic tongs
A technology of complex body and exhaust pipe, which is applied in the field of metal composite material processing, can solve the problems of low yield rate and air leakage of the jacket body, and achieve the effects of high yield rate, good quality of clamp seal, and stable process
- Summary
- Abstract
- Description
- Claims
- Application Information
AI Technical Summary
Problems solved by technology
Method used
Examples
Embodiment 1
[0033] Vacuum electron beam welding is carried out between the degassing pipe and the upper cover of the composite package, and the vacuum degree of vacuum electron beam welding is 3×10 -5 MPa, welding current B=80mA, welding speed F=300° / min, focusing current Z=6000mA, and then carry out vacuum electron beam welding on the upper and lower covers of the composite sheath and the composite sheath body, firstly the upper cover , The gap between the lower cover and the bag is welded at eight points, and the vacuum degree of the vacuum electron beam furnace chamber is 3×10 -5 MPa, welding current B=80mA, welding speed F=300° / min, focusing current Z=6000mA, check the quality of solder joints, and conduct vacuum electron beam sealing welding after confirmation, welding current B=90mA, welding speed F=200° / min, focusing current Z=6000mA, to obtain the welded composite package; put the welded NbTi / Cu composite package with a diameter of Φ350mm and a length of 920mm into the degassing ...
Embodiment 2
[0035] Vacuum electron beam welding is carried out between the degassing pipe and the upper cover of the composite package, and the vacuum degree of vacuum electron beam welding is 6×10 -7 MPa, welding current B=80mA, welding speed F=300° / min, focusing current Z=6000mA, and then carry out vacuum electron beam welding on the upper and lower covers of the composite sheath and the sheath respectively. The gap between the cover and the cover is welded at eight points, and the vacuum degree of the vacuum electron beam furnace chamber is 6×10 -7 MPa, welding current B=80mA, welding speed F=300° / min, focusing current Z=6000mA, check the quality of solder joints, and conduct vacuum electron beam sealing welding after confirmation, welding current B=90mA, welding speed F=200° / min, focusing current Z=6000mA, to obtain the welded complex sheath; the welded Nb with a diameter of Φ120mm and a length of 240mm 3 The Al complex package is put into the degassing furnace, and the vacuum unit ...
Embodiment 3
[0037] Vacuum electron beam welding is performed on the degassing pipe and the upper cover of the composite package, and the vacuum degree of vacuum electron beam welding is 5×10 -6 MPa, welding current B=80mA, welding speed F=300° / min, focusing current Z=6000mA, and then carry out vacuum electron beam welding on the upper and lower covers of the composite sheath and the sheath respectively. The gap between the cover and the jacket is welded at eight points, and the vacuum degree of the vacuum electron beam furnace chamber is 5×10 -6MPa, welding current B=80mA, welding speed F=300° / min, focusing current Z=6000mA, check the quality of solder joints, and conduct vacuum electron beam sealing welding after confirmation, welding current B=90mA, welding speed F=200° / min, focusing current Z=6000mA, to obtain the welded composite package; put the welded NbTi / Cu composite package with a diameter of Φ350mm and a length of 920mm into the degassing furnace, and vacuum the vacuum unit wit...
PUM
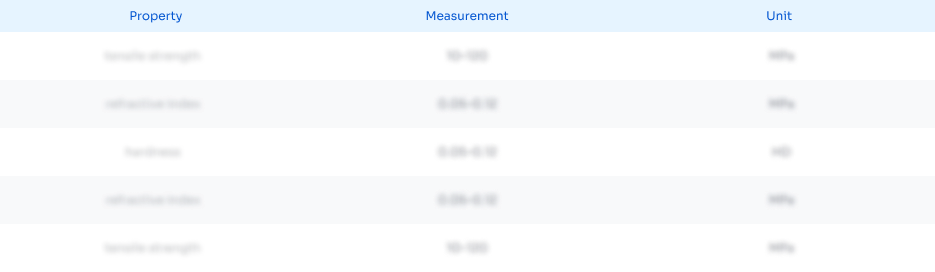
Abstract
Description
Claims
Application Information

- R&D Engineer
- R&D Manager
- IP Professional
- Industry Leading Data Capabilities
- Powerful AI technology
- Patent DNA Extraction
Browse by: Latest US Patents, China's latest patents, Technical Efficacy Thesaurus, Application Domain, Technology Topic, Popular Technical Reports.
© 2024 PatSnap. All rights reserved.Legal|Privacy policy|Modern Slavery Act Transparency Statement|Sitemap|About US| Contact US: help@patsnap.com