Aluminium alloy engine cast iron cylinder sleeve processing technology
A treatment process, aluminum alloy technology, applied in metal material coating process, hot-dip plating process, coating, etc., can solve the problem of wear resistance and strength damage of cast iron cylinder liner, short processing time of aluminum alloy melt and metallurgical combination To achieve the effect of improving the performance of the bonding surface, inhibiting the reaction of zinc and iron, and improving the bonding interface
- Summary
- Abstract
- Description
- Claims
- Application Information
AI Technical Summary
Problems solved by technology
Method used
Image
Examples
Embodiment 1
[0030] Raw materials include: HT250 cast iron cylinder liner, industrial ZL101A aluminum alloy, zinc aluminum alloy and self-prepared flux (mainly composed of zinc chloride ZnCl 2 , potassium fluoride KF, potassium chloride KCl, sodium nitrate NaNO 3 , sodium nitrite NaNO 2 , ferrous dihydrogen phosphate Fe(H 2 PO 4 ) 2 and surfactant CH 3 (CH 2 ) 11 SO 3 Na).
[0031] (1) Use HT250 cast iron as the cylinder liner, the outer surface of the HT250 cast iron cylinder liner is first degreased, shot blasted or other mechanically polished to remove rust and free carbon on the surface;
[0032] (2) prepare plating flux, take by weighing zinc chloride ZnCl respectively by the mass percent of salt 45%, 24.9%, 20%, 3%, 2%, 5%, 0.1% 2 , potassium fluoride KF, potassium chloride KCl, sodium nitrate NaNO 3 , sodium nitrite NaNO 2 , ferrous dihydrogen phosphate Fe(H 2 PO 4 ) 2 , Surfactant CH 3 (CH 2 ) 11 SO 3 Na, prepare it with deionized water to make a salt solution wit...
Embodiment 2
[0039] Raw materials include: HT250 cast iron cylinder liner, industrial ZL101A aluminum alloy, zinc aluminum alloy and self-prepared flux (mainly composed of zinc chloride ZnCl 2 , potassium fluoride KF, potassium chloride KCl, sodium nitrate NaNO 3 , sodium nitrite NaNO 2 , ferrous dihydrogen phosphate Fe(H 2 PO 4 ) 2 and surfactant CH 3 (CH 2 ) 11 SO 3 Na).
[0040] (1) Use HT250 cast iron as the cylinder liner, the outer surface of the HT250 cast iron cylinder liner is first degreased, shot blasted or other mechanically polished to remove rust and free carbon on the surface;
[0041] (2) Prepare plating flux, take zinc chloride ZnCl by weighing 45%, 22%, 19.7%, 5%, 3%, 5%, 0.3% by mass percentage of salt 2 , potassium fluoride KF, potassium chloride KCl, sodium nitrate NaNO 3 , sodium nitrite NaNO 2 , ferrous dihydrogen phosphate Fe(H 2 PO 4 ) 2 , Surfactant CH 3 (CH 2 ) 11 SO 3 Na, prepare it with deionized water to make a salt solution with a concentrat...
Embodiment 3
[0048] Raw materials include: HT250 cast iron cylinder liner, industrial ZL101A aluminum alloy, zinc aluminum alloy and self-prepared plating flux (zinc chloride ZnCl 2 , potassium fluoride KF, potassium chloride KCl, sodium nitrate NaNO 3 , sodium nitrite NaNO 2 , ferrous dihydrogen phosphate Fe(H 2 PO 4 ) 2 and surfactant CH 3 (CH 2 ) 11 SO 3 Na.
[0049] (1) Use HT250 cast iron as the cylinder liner, the outer surface of the HT250 cast iron cylinder liner is first degreased, shot blasted or other mechanically polished to remove rust and free carbon on the surface;
[0050] (2) Prepare plating flux, take zinc chloride ZnCl by mass percentage 44%, 24.5%, 20%, 5%, 3%, 4%, 0.5% 2 , potassium fluoride KF, potassium chloride KCl, sodium nitrate NaNO 3 , sodium nitrite NaNO 2 , ferrous dihydrogen phosphate Fe(H 2 PO 4 ) 2 , Surfactant CH 3 (CH 2 ) 11 SO 3 Na, prepare it with deionized water to make a salt solution with a concentration of 100g / L, then immerse the ...
PUM
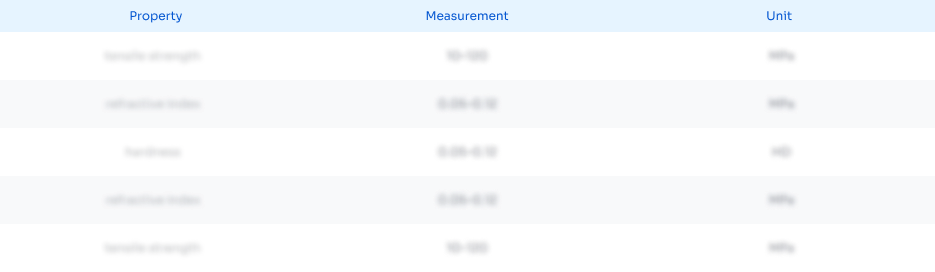
Abstract
Description
Claims
Application Information

- R&D Engineer
- R&D Manager
- IP Professional
- Industry Leading Data Capabilities
- Powerful AI technology
- Patent DNA Extraction
Browse by: Latest US Patents, China's latest patents, Technical Efficacy Thesaurus, Application Domain, Technology Topic, Popular Technical Reports.
© 2024 PatSnap. All rights reserved.Legal|Privacy policy|Modern Slavery Act Transparency Statement|Sitemap|About US| Contact US: help@patsnap.com