Converter steelmaking process for recycling converter final slag
A converter steelmaking and converter technology, which is used in the improvement of process efficiency and the manufacture of converters, etc., can solve the problems of lack of iron and steel, enrichment of impurity elements, and inability to greatly reduce the consumption of iron and steel materials, so as to reduce the consumption and improve the metal consumption. Yield effect
- Summary
- Abstract
- Description
- Claims
- Application Information
AI Technical Summary
Problems solved by technology
Method used
Examples
Embodiment
[0024] Smelting plan: use 100t converter for smelting, add converter final slag cold material 0-70kg / t before adding iron, add about 0-30kg / t of slag and lime in the first batch, add ore and other chemical slag, pour out the amount of slag when pouring slag Above 1 / 3, add lime 20-4-kg / t to two batches of slag. End-point low-temperature control, the target carbon-drawing temperature is 1650°C, after tapping is completed, slag is splashed to protect the furnace and then slag is left.
[0025] The loading amount of molten iron is 101t, 99t, and the amount of scrap steel is 8t, 11t respectively;
[0026] Table 1 main components of molten iron (mass percentage %, balance is Fe)
[0027] the case
steel type
C
Si
mn
P
S
Hot metal temperature ℃
1
Q345R
4.67
0.50
0.14
0.088
0.035
1293
2
D36-1
4.45
0.48
0.12
0.085
0.028
1302
[0028] Table 2 Addition amount of auxiliary ra...
PUM
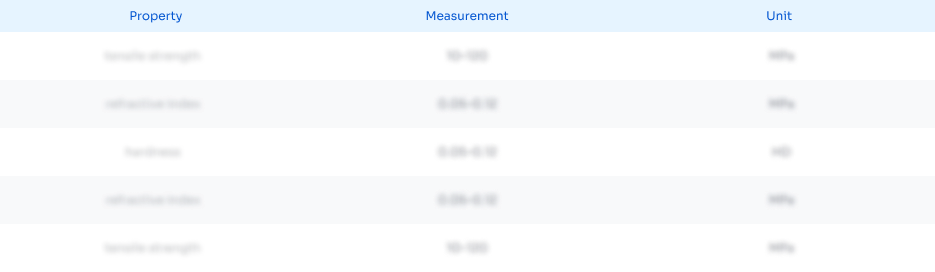
Abstract
Description
Claims
Application Information

- R&D Engineer
- R&D Manager
- IP Professional
- Industry Leading Data Capabilities
- Powerful AI technology
- Patent DNA Extraction
Browse by: Latest US Patents, China's latest patents, Technical Efficacy Thesaurus, Application Domain, Technology Topic, Popular Technical Reports.
© 2024 PatSnap. All rights reserved.Legal|Privacy policy|Modern Slavery Act Transparency Statement|Sitemap|About US| Contact US: help@patsnap.com