A method for preparing phenyldisilane from organosilicon high boilers
A technology of phenyldisilane and high boilers, applied in the field of organosilicon monomer preparation, can solve the problems of increasing reaction and operation difficulty, unfavorable industrial production, increasing production cost, etc., and achieves increasing high-value utilization, increasing Market application, the effect that is beneficial to industrial production
- Summary
- Abstract
- Description
- Claims
- Application Information
AI Technical Summary
Problems solved by technology
Method used
Examples
Embodiment 1
[0037] Rectify the organosilicon high-boiler, take the fraction at 150°C, and obtain Me 4 Cl 2 Si 2 . Under the protection of nitrogen, add 23g Na to 115g toluene, add 1.15g liquid paraffin at the same time, stir and heat to 100°C to prepare sodium sand, add 56.3g chlorobenzene to the prepared sodium sand, and react for 2 hours to obtain Sodium phenyl, add sodium phenyl to 93.5g Me 4 Cl2 Si 2 , while adding 1.87g H(OCH 2 CH 2 ) 3 OH, under the condition of 10°C, after reacting for 3 hours, stop the reaction, cool to room temperature, filter the reaction solution, sample the filtrate, analyze it by gas chromatography, and calculate Me 4 PhSi 2 The yield of Cl is 85.7%, Me 4 Ph 2 Si 2 The yield is 3.8%, and the total yield of target product phenyldisilane with active groups is 89.4%.
Embodiment 2
[0039] Rectify the organosilicon high-boiler, take the fraction at 150°C, and obtain Me 3 Cl 3 Si 2 with Me 4 Cl 2 Si 2 of the mixture. Under the protection of neon gas, add 15g Na and Li alloy to 150g toluene, add 1.5g stearic acid at the same time, stir and heat to 105°C to prepare alkali metal sand, add 78.5g bromobenzene to the prepared alkali metal sand In the sand, reaction equilibrium 2h, obtains phenyl alkali metal salt; The phenyl alkali metal salt is added to 46.8g Me 4 Cl 2 Si 2 , while adding 0.936g H(OCH 2 CH 2 ) 5 OH and 15-C-5 mixed cocatalyst, under the condition of 40 ℃, after reacting for 3 hours, stop the reaction, cool to room temperature, filter the reaction solution, sample the filtrate, analyze it by gas chromatography, and calculate Me 4 PhSi 2 Cl yield is 81.1%, Me 4 Ph 2 Si 2 The yield was 4%, and the total yield of the target product phenyldisilane with active groups was 85.2%.
Embodiment 3
[0041] Rectify the organosilicon high boiler, and take the fraction at 165°C to obtain Me 4 Cl 2 Si 2 with Me 3 Cl 3 Si 2 of mixed components. Under the protection of helium, add 39g K to 390g toluene, add 2.6g oleic acid at the same time, stir and heat to 102°C to prepare potassium sand, add potassium sand to 82.5g Me 4 Cl 2 Si 2 with Me 3 Cl 3 Si 2 Add 0.83g of cyclodextrin and tetraphenylphosphine chloride as a mixing aid to the mixed solution and 56.3g of chlorobenzene mixed solution. After reacting for 4 hours at 30°C, stop the reaction and cool to room temperature. Filter, sample the filtrate, analyze it with gas chromatography, and calculate Me 4 PhSi 2 The yield of Cl is 27.9%, Me 4 Ph 2 Si 2 The yield is 6%, Me 3 PhSi 2 Cl 2 Yield is 39.1%, Me 3 Ph 2 Si 2 The Cl yield is 19%, and the total yield of the target product phenyldisilane with active groups is 86%.
PUM
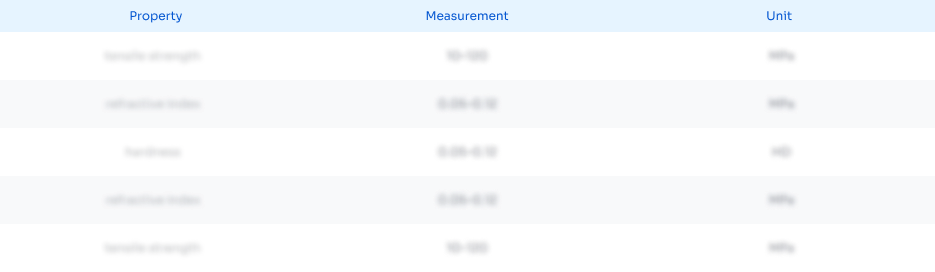
Abstract
Description
Claims
Application Information

- R&D
- Intellectual Property
- Life Sciences
- Materials
- Tech Scout
- Unparalleled Data Quality
- Higher Quality Content
- 60% Fewer Hallucinations
Browse by: Latest US Patents, China's latest patents, Technical Efficacy Thesaurus, Application Domain, Technology Topic, Popular Technical Reports.
© 2025 PatSnap. All rights reserved.Legal|Privacy policy|Modern Slavery Act Transparency Statement|Sitemap|About US| Contact US: help@patsnap.com