Method for preparing iron oxide red by using copper nickel slag
A technology for red iron oxide and copper-nickel slag is applied in the field of mineral resource recycling, which can solve the problems of non-recycling of pickling waste liquid, high roasting temperature and complicated process, and achieve fast and effective solid-liquid separation and high product purity. , the effect of preventing environmental pollution
- Summary
- Abstract
- Description
- Claims
- Application Information
AI Technical Summary
Problems solved by technology
Method used
Image
Examples
Embodiment 1
[0051] Step 1: adopt the closed-circuit grinding scheme, feed the copper-nickel slag through the vibrating feeder, and send it into the mill by the belt conveyor; after reaching the particle size requirement of 70-75%-80 mesh, it is lifted by the screw conveyor and bucket The machine is lifted to the powder silo for standby; the main component content of the copper-nickel slag is shown in Table 1; the copper waste slag that has been ground in the powder silo is weighed and then added to the first-stage leaching tank, and water is added in proportion. and sulfuric acid, the amount of sulfuric acid added is 1.1 times the theoretical molar amount of iron in the copper-nickel slag, the mass percentage concentration of sulfuric acid in the pulp is maintained at 80% during leaching, and the temperature is 50°C for 30 minutes; the pulp that has been leached in the first stage Quickly pour into the second-stage stirring leaching tank, and at the same time add water in proportion to kee...
Embodiment 2
[0060] Step 1: adopt the closed-circuit grinding scheme, feed the copper-nickel slag through the vibrating feeder, and send it into the mill by the belt conveyor; after reaching the particle size requirement of 70-75%-200 mesh, it is lifted by the screw conveyor and bucket The machine is lifted to the powder silo for standby. The main component content of copper-nickel slag is shown in Table 2; weigh 100kg of the copper waste slag that has been ground in the powder silo and add it to the first-stage leaching tank, and add water and hydrochloric acid in proportion at the same time. The amount of hydrochloric acid added is The theoretical molar amount of iron in copper-nickel slag is 0.9 times, and the mass percentage concentration of hydrochloric acid in the pulp is kept at 35% during leaching, and the temperature is 70°C for 30 minutes; the pulp that has been leached in the first stage is quickly poured into the second stage for stirring At the same time, water is added in pro...
Embodiment 3
[0068] Step 1: adopt the closed-circuit grinding scheme, feed the copper-nickel slag through the vibrating feeder, and send it into the mill by the belt conveyor; after reaching the particle size requirement of 80-85%-325 mesh, it is lifted by the screw conveyor and bucket The machine is lifted to the powder silo for standby use; the main component content of the copper-nickel slag is shown in Table 3; 100 kg of copper waste slag that has been ground in the powder silo is weighed and then added to the first-stage leaching tank, and simultaneously added in proportion Water and nitric acid, the amount of nitric acid added is 1.4 times the theoretical molar amount of iron in the copper-nickel slag, the mass percentage concentration of nitric acid in the pulp is maintained at 50% during leaching, and the temperature is 70 °C for 90 minutes; the first-stage leached The ore pulp is quickly poured into the second-stage stirring leaching tank, and water is added in proportion at the sa...
PUM
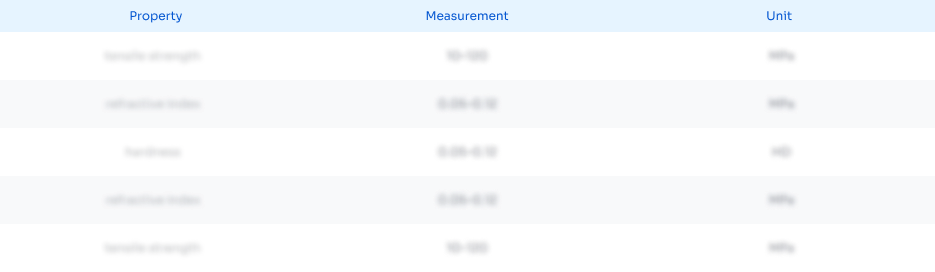
Abstract
Description
Claims
Application Information

- R&D
- Intellectual Property
- Life Sciences
- Materials
- Tech Scout
- Unparalleled Data Quality
- Higher Quality Content
- 60% Fewer Hallucinations
Browse by: Latest US Patents, China's latest patents, Technical Efficacy Thesaurus, Application Domain, Technology Topic, Popular Technical Reports.
© 2025 PatSnap. All rights reserved.Legal|Privacy policy|Modern Slavery Act Transparency Statement|Sitemap|About US| Contact US: help@patsnap.com