Composite building block as well as production mold and production method thereof
A composite and block technology, applied in the field of wall masonry materials, can solve problems such as high water absorption, unstable quality, and settlement
- Summary
- Abstract
- Description
- Claims
- Application Information
AI Technical Summary
Problems solved by technology
Method used
Image
Examples
Embodiment Construction
[0051] The present invention as Figure 1-14 As shown, it includes a load-bearing matrix 2 and at least one thermal insulation body 1; the composite material and "embedded" structure not only ensure the overall strength of the block, but also improve the thermal insulation effect of the block.
[0052] The insulation body 1 is composed of 40-60% cement, 8-15% silica fume, 3-5% hydrogen peroxide, 0.5-1% modifier and 31-38% water by weight percentage;
[0053] The load-bearing matrix 2 is composed of 20-40% of cement, 0-40% of tailings sand, 25-65% of recycled construction waste raw materials, 10-40% of fly ash, 3-5% of fibrous rod-shaped materials, peroxidized Composed of 0.10-0.40% hydrogen, 0.7-1.6% admixture and 20-36% water;
[0054] Among them, silica fume is an ultrafine silicon powder material formed by rapid oxidation and condensation of SiO2 and Si gas produced during smelting ferrosilicon alloy and industrial silicon and oxygen in the air. Silica fume has a large sp...
PUM
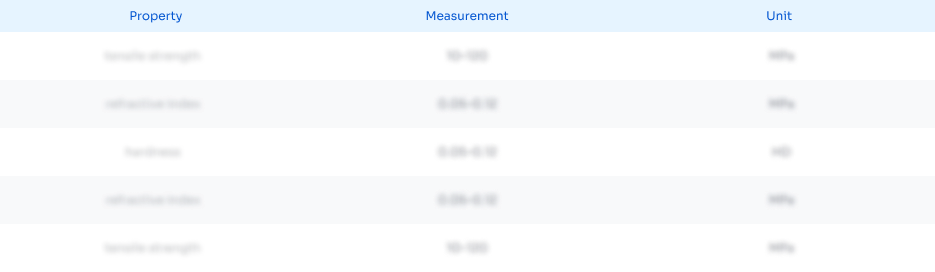
Abstract
Description
Claims
Application Information

- R&D
- Intellectual Property
- Life Sciences
- Materials
- Tech Scout
- Unparalleled Data Quality
- Higher Quality Content
- 60% Fewer Hallucinations
Browse by: Latest US Patents, China's latest patents, Technical Efficacy Thesaurus, Application Domain, Technology Topic, Popular Technical Reports.
© 2025 PatSnap. All rights reserved.Legal|Privacy policy|Modern Slavery Act Transparency Statement|Sitemap|About US| Contact US: help@patsnap.com