A pollution-free preparation process of a wide temperature coal-to-natural gas methanation catalyst
A methanation catalyst and coal-to-natural gas technology, applied in the petroleum industry, gas fuel, fuel, etc., can solve the problems of waste water and gas discharge
- Summary
- Abstract
- Description
- Claims
- Application Information
AI Technical Summary
Problems solved by technology
Method used
Image
Examples
Embodiment 1
[0034] 1. Take 786g of nickel nitrate and dissolve it in 5400g of deionized water, then add 270g of isopropanol to get the bottom solution;
[0035] 2. Add MgAl to the bottom liquid 2 o 4 142g of porous magnesium aluminate is fully beaten;
[0036] 3. Preheat the slurry to 90°C;
[0037] 4. Add 95g of carbonyl nickel powder;
[0038] 5. Inject air into the hydrogen peroxide storage tank containing 2.0 mol at a rate of 0.5 L / min to obtain air saturated with hydrogen peroxide;
[0039] 6. Pass the above-mentioned air saturated with hydrogen peroxide into the slurry in step 4);
[0040] 7. After the hydrogen peroxide volatilizes, age the reacted slurry at 80°C for 12 hours, and then filter to obtain a filter cake;
[0041] 8. The filter cake is dried at 80°C, crushed, pressed into tablets, and roasted at 550°C to obtain a wide-temperature coal-to-natural gas methanation catalyst;
[0042] 9. The air from step 6) is circulated repeatedly by the fan until the hydrogen peroxid...
Embodiment 2
[0046] 1. Take 2600g nickel nitrate and dissolve it in 5400g deionized water, then add 80g tert-butanol to get the bottom solution;
[0047] 2. Add MgAl to the bottom liquid 2 o 4 142g of porous magnesium aluminate and 142g of CeO 2 Fully beat;
[0048] 3. Preheat the slurry to 60°C;
[0049] 4. Add 122g of sponge nickel powder;
[0050] 5. Pass air into the hydrogen peroxide storage tank containing 2.5 mol at a rate of 1.5 L / min to obtain air saturated with hydrogen peroxide;
[0051] 6. Pass the above-mentioned air saturated with hydrogen peroxide into the slurry in step 4);
[0052] 7. After the hydrogen peroxide volatilizes, age the reacted slurry at 60°C for 12 hours, and then filter to obtain a filter cake;
[0053] 8. The filter cake is dried at 200°C, crushed, pressed into tablets, and roasted at 800°C to obtain a wide-temperature coal-to-natural gas methanation catalyst;
[0054] 9. The air from step 6) is circulated repeatedly by the fan until the hydrogen per...
Embodiment 3
[0058] 1. Take 1571g of nickel nitrate and dissolve it in 5400g of deionized water, then add 108g of neopentyl alcohol to get the bottom solution;
[0059] 2. Add 213g of La to the above bottom liquid 2 o 3 Fully beat;
[0060]3. Preheat the slurry to 100°C;
[0061] 4. Add 142g of sponge nickel powder;
[0062] 5. Pass air into the hydrogen peroxide storage tank containing 3.0 mol at a rate of 1.5 L / min to obtain air saturated with hydrogen peroxide;
[0063] 6. Pass the above-mentioned air saturated with hydrogen peroxide into the slurry in step 4);
[0064] 7. After the hydrogen peroxide volatilizes, age the reacted slurry at 100°C for 1 hour, and then filter to obtain a filter cake;
[0065] 8. The filter cake is dried at 120°C, crushed, pressed into tablets, and roasted at 600°C to obtain a wide-temperature coal-to-natural gas methanation catalyst;
[0066] 9. The air from step 6) is circulated repeatedly by the fan until the hydrogen peroxide content is less than 1...
PUM
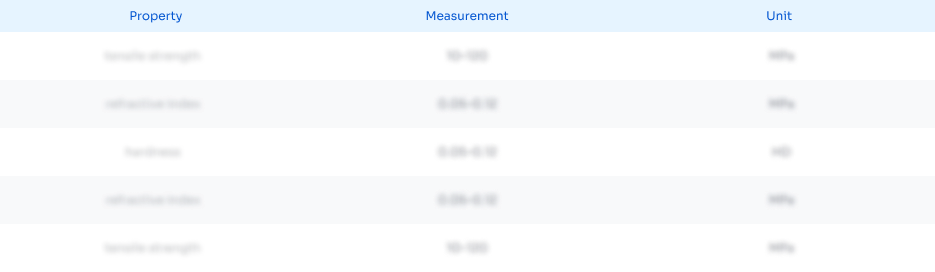
Abstract
Description
Claims
Application Information

- Generate Ideas
- Intellectual Property
- Life Sciences
- Materials
- Tech Scout
- Unparalleled Data Quality
- Higher Quality Content
- 60% Fewer Hallucinations
Browse by: Latest US Patents, China's latest patents, Technical Efficacy Thesaurus, Application Domain, Technology Topic, Popular Technical Reports.
© 2025 PatSnap. All rights reserved.Legal|Privacy policy|Modern Slavery Act Transparency Statement|Sitemap|About US| Contact US: help@patsnap.com