Preparation method for aluminum-plated paper packaging material for cigarettes
A packaging material and aluminized paper technology, applied in the field of packaging materials, can solve the problems of difficult to control product color difference, poor surface finish of aluminized paper, rough nitrocellulose coating, etc., and achieve the effect of reducing production costs
- Summary
- Abstract
- Description
- Claims
- Application Information
AI Technical Summary
Problems solved by technology
Method used
Examples
Embodiment 1
[0015] A method for preparing aluminized paper packaging material for cigarettes, the method comprising the steps of:
[0016] 1) Coating a release coating on the polyester film and drying it at 142°C to form an easy-release coating with a thickness of 2g / square meter; wherein the composition of the release coating is: acetate fiber 18-22% plain resin, 7-9% divinyl chloride resin, 24-26% acrylic resin, 1.5-2.5% polypropylene wax, 1-2% dioctyl phthalate, titanate coupling agent 0.5-1.5%, 2-hydroxy-4-methoxybenzophenone 0.2-0.4%, dibutyltin dilaurate 0.1-0.2%, the balance is butanone;
[0017] 2) Heat and melt metal aluminum in a vacuum environment, and spray it on the above-mentioned easy-peelable coating to form a vacuum aluminized transfer film;
[0018] 3) Apply an adhesive on the aluminum film of the aluminized transfer film and paste a composite paper layer, dry at 60°C, and then cool and solidify at room temperature to form a composite semi-finished product;
[0019] 4)...
Embodiment 2
[0021] A method for preparing aluminized paper packaging material for cigarettes, the method comprising the steps of:
[0022] 1) Coating a stripping coating on the polyester film and drying it at 146°C to form an easy-peeling coating with a thickness of 1.9g / square meter; wherein the composition of the stripping coating is: acetic acid Cellulose resin 18-22%, dibasic vinyl chloride resin 7-9%, acrylic resin 24-26%, polypropylene wax 1.5-2.5%, dioctyl phthalate 1-2%, titanate coupling Agent 0.5-1.5%, 2-hydroxy-4-methoxybenzophenone 0.2-0.4%, dibutyltin dilaurate 0.1-0.2%, the balance is butanone;
[0023] 2) Heat and melt metal aluminum in a vacuum environment, and spray it on the above-mentioned easy-peelable coating to form a vacuum aluminized transfer film;
[0024] 3) Apply an adhesive on the aluminum film of the aluminized transfer film and paste a composite paper layer, dry at 90°C, and then cool and solidify at room temperature to form a composite semi-finished product...
Embodiment 3
[0027] A method for preparing aluminized paper packaging material for cigarettes, the method comprising the steps of:
[0028] 1) Coating a stripping coating on a polyester film and drying it at 144°C to form an easy-peeling coating with a thickness of 1.95g / square meter; wherein the composition of the stripping coating is in weight percent: acetic acid Cellulose resin 18-22%, dibasic vinyl chloride resin 7-9%, acrylic resin 24-26%, polypropylene wax 1.5-2.5%, dioctyl phthalate 1-2%, titanate coupling Agent 0.5-1.5%, 2-hydroxy-4-methoxybenzophenone 0.2-0.4%, dibutyltin dilaurate 0.1-0.2%, the balance is butanone;
[0029] 2) Heat and melt metal aluminum in a vacuum environment, and spray it on the above-mentioned easy-peelable coating to form a vacuum aluminized transfer film;
[0030] 3) Apply an adhesive on the aluminum film of the aluminized transfer film and paste a composite paper layer, dry at 75°C, and then cool and solidify at room temperature to form a composite semi...
PUM
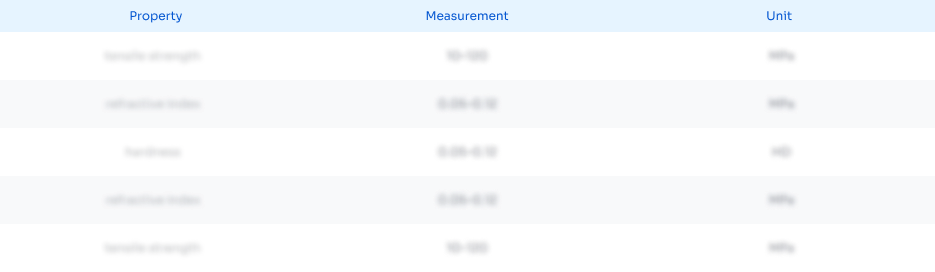
Abstract
Description
Claims
Application Information

- Generate Ideas
- Intellectual Property
- Life Sciences
- Materials
- Tech Scout
- Unparalleled Data Quality
- Higher Quality Content
- 60% Fewer Hallucinations
Browse by: Latest US Patents, China's latest patents, Technical Efficacy Thesaurus, Application Domain, Technology Topic, Popular Technical Reports.
© 2025 PatSnap. All rights reserved.Legal|Privacy policy|Modern Slavery Act Transparency Statement|Sitemap|About US| Contact US: help@patsnap.com