Magnetic hardening FeGa alloy and preparation method thereof
A technology of alloy and magnetic field strength, applied in the manufacture/assembly of magnetostrictive devices, material selection for magnetostrictive devices, device material selection, etc., can solve the problems of high temperature failure, high demagnetization rate, closing and opening current Higher problems, to achieve low demagnetization rate, improve reliability, and reduce the effect of opening and closing current
- Summary
- Abstract
- Description
- Claims
- Application Information
AI Technical Summary
Problems solved by technology
Method used
Image
Examples
preparation example Construction
[0037]Under the prior art, different heat treatment methods for iron-based alloys can form different types of magnetic hardening alloys such as quenched steel type, α / γ phase transformation type, metastable phase decomposition type and precipitation type. The inventors of the present invention have found that micro-alloying and directional casting to prepare oriented FeGa alloys, and finally magnetizing with superconducting strong magnets is another new way of magnetic hardening of FeGa alloys. Directional casting can obtain unidirectionally grown crystals whose growth direction is consistent with the principal stress direction, eliminate transverse grain boundaries, improve the unidirectional mechanical strength of the alloy, and more importantly, lay a solid foundation for subsequent magnetization and magnetic retention. Base. Concrete preparation method comprises the following steps:
[0038] (1) Smelting and casting: First weigh Ga, C, Mn and Fe and other raw materials an...
Embodiment 1
[0043] Raw materials such as Fe, Ga, Mn, C with a purity greater than 99.9% are weighed with an electronic balance, according to the mass percentage Ga: 1.00wt%, C: 0.46wt%, Mn: 0.68wt%, and the Fe balance is weighed and placed into the water-cooled copper crucible in the vacuum induction furnace, and adjust the vacuum degree of the vacuum chamber to 4×10 -3 Pa, introduce high-purity argon as a protective gas, adjust the heating power to completely melt the raw materials, then rapidly solidify them into alloy ingots in a water-cooled copper crucible, and then turn over the alloy ingots for melting. The composition is uniform, and then cast into a mold with a water-cooled copper bottom for directional casting into a FeGa alloy billet.
[0044] Put the FeGa alloy billet into the vacuum heat treatment furnace, and adjust the vacuum degree of the vacuum chamber to (2~4)×10 -3 Pa, and then pass inert gas such as argon as protective gas, the pressure is 5×10 4 Pa, in a protective ...
Embodiment 2
[0049] Firstly weigh Fe, Ga, Mn, C and other raw materials with a purity greater than 99.9% with an electronic balance, according to the mass percentage Ga: 10.00wt%, C: 0.45wt%, Mn: 0.72wt%, after weighing the Fe balance Put it into a water-cooled copper crucible in a vacuum induction furnace, and adjust the vacuum degree of the vacuum chamber to 3×10 -3 Pa, and then pass inert gas such as high-purity argon as a protective gas, adjust the heating power to completely melt the raw material, then make it quickly solidify into an alloy ingot in a water-cooled copper crucible, and then turn over the alloy ingot for melting, so repeatedly smelting for 4 Make the composition of the alloy uniform for the first time, and then cast it into a mold with a water-cooled copper bottom to form a FeGa alloy billet.
[0050] Put the FeGa alloy billet into the vacuum heat treatment furnace, and adjust the vacuum degree of the vacuum chamber to (2~4)×10 -3 Pa, and then pass inert gas such as ar...
PUM
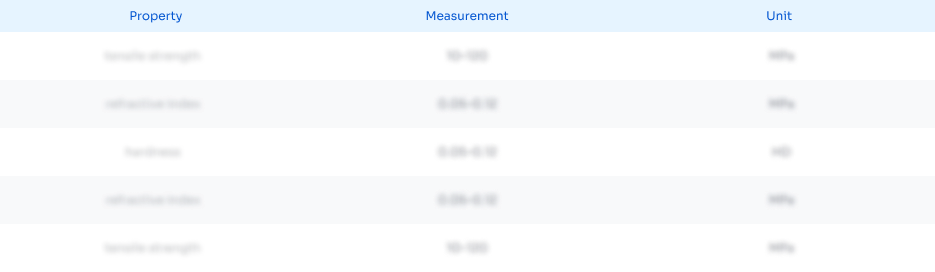
Abstract
Description
Claims
Application Information

- R&D Engineer
- R&D Manager
- IP Professional
- Industry Leading Data Capabilities
- Powerful AI technology
- Patent DNA Extraction
Browse by: Latest US Patents, China's latest patents, Technical Efficacy Thesaurus, Application Domain, Technology Topic, Popular Technical Reports.
© 2024 PatSnap. All rights reserved.Legal|Privacy policy|Modern Slavery Act Transparency Statement|Sitemap|About US| Contact US: help@patsnap.com