Manufacturing technology method of automobile motor fan housing
A production process and fan cover technology, applied in the field of automobile motor fan cover production technology, can solve the problems of unstable injection molding conditions, product collision and scratches, low drying temperature, etc., to reduce whitening and scratches, and prolong drying. The effect of temperature, electrothermal temperature increase
- Summary
- Abstract
- Description
- Claims
- Application Information
AI Technical Summary
Problems solved by technology
Method used
Examples
Embodiment 1
[0023] According to the technical solution provided by the present invention, the raw material used for the fan cover of the automobile motor is PP+T30%. Before injection molding, the raw material is placed in an oven at 70°C, dried for 4 hours, and the dried raw material is put into the injection molding machine. , set the pressure of the first section of the injection molding machine to 1658.3 Kg / cm 2 , the second stage pressure is 1658.3Kg / cm 2 , the three-stage pressure is 1658.3 Kg / cm 2 , the four-stage pressure is 1539.85 Kg / cm 2 , the injection speed of the first stage is 9.84mm / s, the injection speed of the second stage is 55.35mm / s, the injection speed of the third stage is 55.35mm / s, the injection speed of the fourth stage is 24.6mm / s, the end position of the first stage is 75mm, and the end position of the second stage 56mm, the end position of the third section is 14mm, set the electric heating temperature of the material tube (1 #~7#) of the injection molding ma...
Embodiment 2
[0025] According to the technical solution provided by the present invention, the raw material used for the fan cover of the automobile motor is PP+T30%. Before injection molding, the raw material is placed in an oven at 80°C, dried for 4 hours, and the dried raw material is put into the injection molding machine. , set the pressure of the first section of the injection molding machine to 1895.2 Kg / cm 2 , the second stage pressure is 1895.2 Kg / cm 2 , the three-stage pressure is 1895.2 Kg / cm 2 , the four-stage pressure is 1776.75 Kg / cm 2 , the injection speed of the first stage is 22.14mm / s, the injection speed of the second stage is 67.65mm / s, the injection speed of the third stage is 67.65mm / s, the injection speed of the fourth stage is 36.9mm / s, the end position of the first stage is 85mm, and the end position of the second stage 66mm, the end position of the third section is 24mm, set the electric heating temperature of the material pipe (1 #~7#) of the injection molding ...
Embodiment 3
[0027] According to the technical solution provided by the present invention, the raw material used for the fan cover of the automobile motor is PP+T30%. Before injection molding, the raw material is placed in an oven at 90°C, dried for 4 hours, and the dried raw material is put into the injection molding machine. , set the pressure of the first section of the injection molding machine to 2132.1Kg / cm 2 , the second stage pressure is 2132.1Kg / cm 2 , the three-stage pressure is 2132.1Kg / cm 2 , the four-stage pressure is 2013.65 Kg / cm 2 , the injection speed of the first stage is 34.44mm / s, the injection speed of the second stage is 79.95mm / s, the injection speed of the third stage is 79.95mm / s, the injection speed of the fourth stage is 49.2mm / s, the end position of the first stage is 95mm, and the end position of the second stage 76mm, the end position of the third section is 34mm, set the electric heating temperature of the material pipe (1 #~7#) of the injection molding mac...
PUM
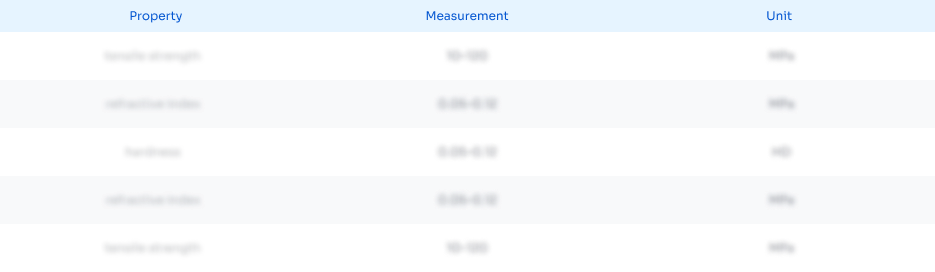
Abstract
Description
Claims
Application Information

- Generate Ideas
- Intellectual Property
- Life Sciences
- Materials
- Tech Scout
- Unparalleled Data Quality
- Higher Quality Content
- 60% Fewer Hallucinations
Browse by: Latest US Patents, China's latest patents, Technical Efficacy Thesaurus, Application Domain, Technology Topic, Popular Technical Reports.
© 2025 PatSnap. All rights reserved.Legal|Privacy policy|Modern Slavery Act Transparency Statement|Sitemap|About US| Contact US: help@patsnap.com