Preparation method of polypropylene with high melt strength
A high melt strength, polypropylene technology, applied in the field of polypropylene preparation, can solve problems such as strong complexing ability, and achieve the effects of easy operation, broad application prospects, and high melt strength
- Summary
- Abstract
- Description
- Claims
- Application Information
AI Technical Summary
Problems solved by technology
Method used
Image
Examples
Embodiment 1
[0044] The polymerization reaction was carried out on a set of 25Kg / hr polypropylene pilot plant. Its main equipment includes prepolymerization reactor, first loop reactor and second loop reactor. Polymerization method and steps are as follows:
[0045] Step I
[0046] Prepolymerization:
[0047]The main catalyst (DQ-III catalyst, provided by Beijing Aoda Branch of Sinopec Catalyst Company), co-catalyst (triethylaluminum), and the first external electron donor (dicyclopentyldimethoxysilane) were tested at 6°C for 20min After pre-contact, continuously add to the continuous stirred tank pre-polymerization reactor for pre-polymerization reactor, the flow rate of triethylaluminum (TEA) entering the pre-polymerization reactor is 6.33g / hr, dicyclopentyldimethoxysilane (DCPMS) flow rate is 0.63g / hr, main catalyst flow rate is 0.01g / hr, TEA / DCPMS ratio is 20 (molar ratio), wherein DCPMS is the first external electron donor. The prepolymerization is carried out in the bulk environm...
Embodiment 2
[0056] Step is with embodiment 1, difference is: in the first loop reactor of step i, add a small amount of hydrogen, the hydrogen concentration that online chromatography detects is 300ppmV, the hydrogen concentration in the second loop reactor of step Ⅲ changes 1000ppmV. Polymerization process conditions, obtained polymer analysis results and polymer physical properties are listed in Tables 1-3.
Embodiment 3
[0058] Step is the same as Example 2, and the difference is: the ratio of aluminum alkyl and external electron donor in the reactor in the two steps is adjusted, and TEA / DCPMS is adjusted to 60 (molar ratio) in the first reactor of step i ), the TEA / DIBMP in the second reactor is adjusted to 10 (molar ratio), and the hydrogen concentration in the second loop reactor of step Ⅲ is changed to 5000ppmV. Polymerization process conditions, obtained polymer analysis results and polymer physical properties are listed in Tables 1-3.
PUM
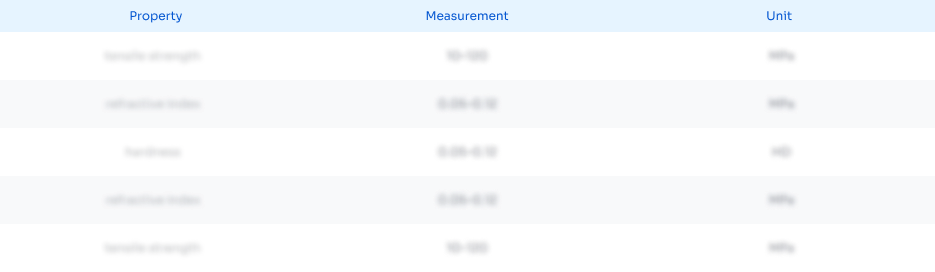
Abstract
Description
Claims
Application Information

- Generate Ideas
- Intellectual Property
- Life Sciences
- Materials
- Tech Scout
- Unparalleled Data Quality
- Higher Quality Content
- 60% Fewer Hallucinations
Browse by: Latest US Patents, China's latest patents, Technical Efficacy Thesaurus, Application Domain, Technology Topic, Popular Technical Reports.
© 2025 PatSnap. All rights reserved.Legal|Privacy policy|Modern Slavery Act Transparency Statement|Sitemap|About US| Contact US: help@patsnap.com