Compound type desulfurization grout and preparation method thereof
A desulfurization slurry and matching technology, applied in the field of desulfurization, can solve the problems of high desulfurization cost and low saturated sulfur capacity, and achieve the effects of high desulfurization efficiency, high sulfur capacity and improved desulfurization efficiency
- Summary
- Abstract
- Description
- Claims
- Application Information
AI Technical Summary
Problems solved by technology
Method used
Examples
Embodiment 1
[0031] The composite desulfurization slurry described in this embodiment is mainly prepared from the following raw materials:
[0032] FeCl 3 ·6H 2 O, 6g;
[0033] Triethanolamine, 9g;
[0034] Ammonium bicarbonate, 1.5g;
[0035] Polyethylene glycol dimethyl ether, 0.03g;
[0036] MF-1 fungicide, 0.03g;
[0037] p-toluenesulfonic acid, 0.3g
[0038]Amorphous iron oxyhydroxide, 15g;
[0039] Further, a method for preparing the compound desulfurization slurry is provided, which includes the following steps:
[0040] (1) Weigh the above-mentioned soluble iron salt, iron salt complexing agent, sulfur precipitant, biological inhibitor, and solution stabilizer in sequence and add them to 240 g of deionized water, mix well to obtain a slurry, and then use the Said basic substance adjusts the pH of said slurry to be 7.5, and reacts for 12h under stirring condition, and makes complexed iron solution;
[0041] (2) Weighing the iron oxyhydroxide with the above weight and adding...
Embodiment 2
[0043] The composite desulfurization slurry described in this embodiment is mainly prepared from the following raw materials:
[0044] FeSO 4 ·7H 2 O, 8g;
[0045] Disodium EDTA, 10g;
[0047] Polyethylene glycol, 0.2g;
[0048] Lauryl dimethyl benzyl ammonium chloride, 0.2g;
[0049] Sorbitol, 1g;
[0050] A mixture of amorphous iron oxyhydroxide and γ-FeOOH at a mass ratio of 1:1, 14g;
[0051] Further, a method for preparing the compound desulfurization slurry is provided, which includes the following steps:
[0052] (1) Weigh the above-mentioned soluble iron salt, iron salt complexing agent, sulfur precipitant, biological inhibitor, and solution stabilizer in sequence and add them to 180 g of deionized water, mix well to obtain a slurry, and then use the The pH of the slurry is adjusted by the alkaline substance to be 8, and the reaction is carried out for 13 hours under agitation to obtain a complex iron solution;
[0053] (2) Weigh...
Embodiment 3
[0055] The composite desulfurization slurry described in this embodiment is mainly prepared from the following raw materials:
[0056] Fe(NO 3 ) 3 9H 2 O, 12g;
[0057] Sodium gluconate, 12g;
[0058] Sodium bicarbonate, 2.4g;
[0059] A mixture of polyethylene glycol dimethyl ether and polyethylene glycol with a mass ratio of 1:1, 0.1 g;
[0060] 3-dodecyloxy-2-hydroxypropyltrimethylammonium chloride, 0.1g;
[0061] Sorbitol, 0.3g;
[0062] δ-FeOOH, 18g;
[0063] Further, a method for preparing the compound desulfurization slurry is provided, which includes the following steps:
[0064] (1) Weigh the above-mentioned soluble iron salt, iron salt complexing agent, sulfur sedimentation agent, biological inhibitor, solution stabilizer in sequence and add them to 300g of deionized water, mix well to obtain a slurry, and then use the The pH of the slurry adjusted by the basic substance is 9, and the reaction is carried out for 12 hours under stirring conditions to obtain a...
PUM
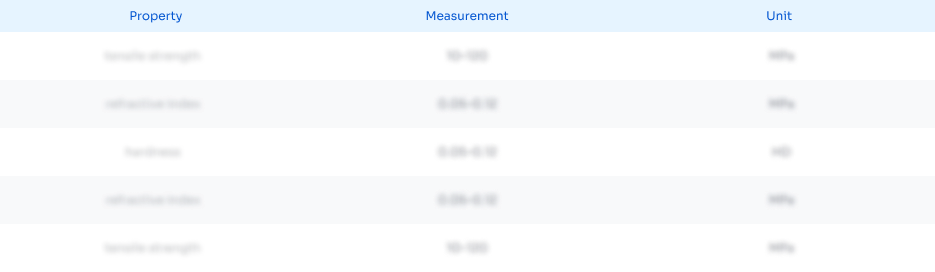
Abstract
Description
Claims
Application Information

- R&D
- Intellectual Property
- Life Sciences
- Materials
- Tech Scout
- Unparalleled Data Quality
- Higher Quality Content
- 60% Fewer Hallucinations
Browse by: Latest US Patents, China's latest patents, Technical Efficacy Thesaurus, Application Domain, Technology Topic, Popular Technical Reports.
© 2025 PatSnap. All rights reserved.Legal|Privacy policy|Modern Slavery Act Transparency Statement|Sitemap|About US| Contact US: help@patsnap.com