Printing and dyeing process of knitted fabric
A printing and dyeing technology, knitted fabric technology, applied in textile decoration, textile material processing, dyeing and other directions, can solve the problems of long process route, difficult quality, high cost, high dye fixation rate, simple operation, environmental pollution small effect
- Summary
- Abstract
- Description
- Claims
- Application Information
AI Technical Summary
Problems solved by technology
Method used
Examples
Embodiment 1
[0016] A printing and dyeing process for knitted fabrics, comprising the steps of:
[0017] 1) Treat gray cloth with 6-7 parts by mass of refining agent, 3-5 parts by mass of hydrogen peroxide, 8-9 parts by mass of alkali, and 4-7 parts by mass of whitening agent, and dehydrate and shape it;
[0018] 2) Take 80-90 parts by mass of guar gum, 1-2 parts by mass of glycerin, and 3-4 parts by mass of 97% sulfuric acid to prepare hollow printing paste, control the viscosity at 30500Pa.S, and pass through a 90-mesh screen; Printing machine printing, the temperature of the machine printing drying room is 120°C, and the burnt-out printing is completed;
[0019] 4) Take 7-8 parts by mass of disperse dye and dissolve it with 25 parts by mass of water, add 2-3 parts by mass of seaweed stock slurry, then add 4-6 parts by mass of anti-staining salt, and finally add 3-6 parts by mass of active The dyestuff is stirred evenly with a high-speed mixer, and the flower paste is prepared; it is pr...
Embodiment 2
[0025] A printing and dyeing process for knitted fabrics, comprising the steps of:
[0026] 1) Take 6 parts by mass of refining agent, 3 parts by mass of hydrogen peroxide, 8 parts by mass of alkali, and 4 parts by mass of whitening agent to treat the gray cloth, dehydrate and shape it;
[0027] 2) Take 80 parts by mass of guardo gum, 1 part by mass of glycerin, and 3 parts by mass of 97% sulfuric acid to prepare a hollow printing paste, control the viscosity at 30500Pa.S, pass through a 90-mesh screen; print with a rotary screen printing machine, machine The temperature of the drying room is 120°C to complete the burnt-out printing;
[0028] 4) Take 7 parts by mass of disperse dye and dissolve it with 25 parts by mass of water, add 2 parts by mass of seaweed stock slurry, then add 4 parts by mass of anti-staining salt, and finally add 3 parts by mass of reactive dye and stir evenly with a high-speed mixer, adjust Prepare and complete the flower paste; print with a rotary scr...
Embodiment 3
[0034] A printing and dyeing process for knitted fabrics, comprising the steps of:
[0035] 1) Take 6.7 parts by mass of refining agent, 3.5 parts by mass of hydrogen peroxide, 8.9 parts by mass of alkali, and 4.7 parts by mass of whitening agent to treat gray cloth, dehydrate and shape it;
[0036] 2) Take 85 parts by mass of guar gum, 1.2 parts by mass of glycerin, and 3.4 parts by mass of 97% sulfuric acid to prepare a hollow printing paste, control the viscosity at 30500Pa.S, pass through a 90-mesh screen; print with a rotary screen printing machine, machine The temperature of the drying room is 120°C to complete the burnt-out printing;
[0037] 4) Take 7.8 parts by mass of disperse dye and dissolve it with 25 parts by mass of water, add 2.3 parts by mass of seaweed stock slurry, then add 4.6 parts by mass of anti-staining salt, and finally add 3.6 parts by mass of reactive dye and stir evenly with a high-speed mixer, adjust Prepare and complete the flower paste; print wi...
PUM
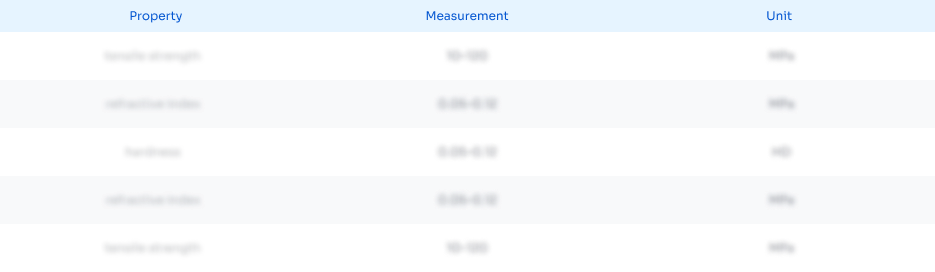
Abstract
Description
Claims
Application Information

- R&D
- Intellectual Property
- Life Sciences
- Materials
- Tech Scout
- Unparalleled Data Quality
- Higher Quality Content
- 60% Fewer Hallucinations
Browse by: Latest US Patents, China's latest patents, Technical Efficacy Thesaurus, Application Domain, Technology Topic, Popular Technical Reports.
© 2025 PatSnap. All rights reserved.Legal|Privacy policy|Modern Slavery Act Transparency Statement|Sitemap|About US| Contact US: help@patsnap.com