Water-based vehicle lamp reflecting cover film-coating paint and preparation method thereof
A reflector, water-based technology, applied in the field of water-based car lamp reflector coating coating and its preparation, can solve the problems of restricted application and high price, and achieve improved heat resistance, improved coating brightness, and good mirror effect Effect
- Summary
- Abstract
- Description
- Claims
- Application Information
AI Technical Summary
Problems solved by technology
Method used
Image
Examples
Embodiment 1
[0029] Add 100g of butyl acrylate (BA), 20g of hydroxyethyl methacrylate (HEMA), 10g of methacrylic acid (MAA), 60g of diacetone alcohol and 60g of n-butanol into the container, and stir at 95-100°C for 5min. Dissolve 2 g of benzoyl peroxide in 30 g of diacetone alcohol, slowly add the dibenzoyl peroxide diacetone alcohol solution dropwise into a reaction container, stir and react at 95-100° C. for 3 hours, and obtain an acrylate resin.
[0030] Dissolve 30g of epoxy resin and 35g of amino resin in a mixed solution of 40g of diacetone alcohol and 20g of n-butanol, slowly add to 120g of the above-mentioned synthesized acrylate resin, stir and mix for 1 hour at 85-90°C, adjust with 25ml of distilled water Paint viscosity and solid content, to obtain water-based paint.
Embodiment 2
[0032] Add 100g of butyl acrylate (BA), 20g of hydroxyethyl methacrylate (HEMA), 10g of methacrylic acid (MAA), 60g of diacetone alcohol and 60g of n-butanol into the container, and stir at 95-100°C for 5min. Dissolve 2 g of benzoyl peroxide in 30 g of diacetone alcohol, slowly add the dibenzoyl peroxide diacetone alcohol solution dropwise into the reaction vessel, stir and react at 95-100° C. for 3 hours to obtain an acrylate resin.
[0033] Dissolve 20g of epoxy resin and 25g of amino resin in a mixed solution of 30g of diacetone alcohol and 15g of n-butanol, slowly add to 120g of the acrylate resin synthesized above, stir and mix for 1 hour at 85-90°C, adjust with 22ml of distilled water Paint viscosity and solid content, to obtain water-based paint.
Embodiment 3
[0035] Add 100g of butyl acrylate (BA), 20g of hydroxyethyl methacrylate (HEMA), 10g of methacrylic acid (MAA), 60g of diacetone alcohol and 60g of n-butanol into the container, and stir at 95-100°C for 5min. Dissolve 2 g of benzoyl peroxide in 30 g of diacetone alcohol, slowly drop the dibenzoyl peroxide diacetone alcohol solution into a reaction vessel, stir and react at 95-100°C for 3 hours, and obtain an acrylate resin.
[0036]Dissolve 15g of epoxy resin and 20g of amino resin in a mixed solution of 20g of diacetone alcohol and 10g of n-butanol, slowly add to 120g of the above-mentioned synthesized acrylate resin, stir and mix for 1 hour at 85-90°C, adjust with 18ml of distilled water Paint viscosity and solid content, to obtain water-based paint.
PUM
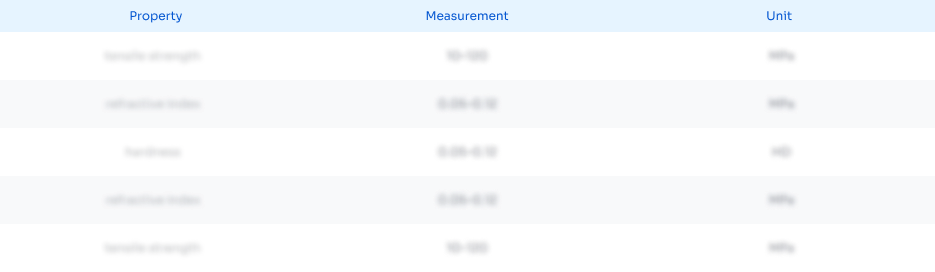
Abstract
Description
Claims
Application Information

- R&D
- Intellectual Property
- Life Sciences
- Materials
- Tech Scout
- Unparalleled Data Quality
- Higher Quality Content
- 60% Fewer Hallucinations
Browse by: Latest US Patents, China's latest patents, Technical Efficacy Thesaurus, Application Domain, Technology Topic, Popular Technical Reports.
© 2025 PatSnap. All rights reserved.Legal|Privacy policy|Modern Slavery Act Transparency Statement|Sitemap|About US| Contact US: help@patsnap.com