Method for comprehensively recovering valuable metals from zinc smelting slag
A technology for valuable metals and zinc smelting slag, which is applied in the field of comprehensive recovery of valuable metals and synchronous recovery of multiple valuable metals from zinc smelting slag, which can solve the secondary pollution of final slag, low comprehensive utilization of resources, heavy metal elements No problems such as solidification have been achieved, and the effect of high recovery rate of valuable metals, strong material adaptability, and comprehensive utilization can be achieved
- Summary
- Abstract
- Description
- Claims
- Application Information
AI Technical Summary
Problems solved by technology
Method used
Image
Examples
Embodiment 1
[0036] Example 1 : Blast furnace slag, alumite slag and lead-silver slag taken from a factory, its chemical composition is respectively: Blast furnace slag: Zn 9.5%, Pb 9.2%, Cu 1.5%, Fe 27.6%, In 15g / t, Ag 33g / t t, Au 1g / t; Lead-silver slag: Zn 6.2%, Pb5.5%, Cu 1.2%, In 210g / t, Ag 195g / t, Au 1g / t; Alumite slag: Zn 4.5%, Pb 4.1% , Cu 0.4%, In 35g / t, Ag 122g / t, Au 1.2g / t. Get respectively 100kg of the above-mentioned blast furnace slag, 200kg of alumina slag, and 100kg of lead-silver slag (the mass ratio of alumina slag: lead-silver slag: blast furnace slag is 1:2:1), and the blast furnace slag, alumina slag and lead-silver slag that will be taken out are The slag was mixed with a tank mixer for 5 minutes, and 20kg of water was added during the mixing process. It was detected that the water content of the mixture was 12%. The mixture was compacted with a hydraulic molding machine, and the agglomerate was dried at 30° C. for 72 hours to obtain 393 kg of dried agglomerate. Add ...
Embodiment 2
[0038] Example 2: Blast furnace slag, jarosite slag and lead-silver slag taken from a factory, their chemical composition are: blast furnace slag: Zn 7.2%, Pb 0.47%, Cu 0.98%, In 31g / t, Ag 24g / t, Au 0.4g / t. Lead-silver slag: Zn 6.9%, Pb 5.9%, Cu 0.42%, In 131g / t, Ag 113g / t, Au 2g / t; Alumite slag: Zn 5.3%, Pb 4.7%, Cu 0.28%, In 45g / t t, Ag 126g / t, Au 0.2g / t. Get respectively 150kg of the above-mentioned blast furnace slag, 300kg of alumina slag, and 100kg of lead-silver slag (the mass ratio of alumina slag: lead-silver slag: blast furnace slag is 1.5:3:1), and the blast furnace slag, alumina slag and lead-silver slag that will be taken out are The slag was mixed with a tank mixer for 8 minutes, and 44kg of water was added during the mixing process. It was detected that the water content of the mixture was 14%. The mixture was compacted with a hydraulic forming machine, and the agglomerate was dried at 100° C. for 48 hours to obtain 517 kg of dried agglomerate. Add 517kg o...
Embodiment 3
[0040] Example 3: Blast furnace slag, alumite slag and lead-silver slag taken from a factory, their chemical composition are: blast furnace slag: Zn 7.5%, Pb 0.43%, Cu 1.01%, In 24g / t, Ag 12g / t, Au 0.3g / t; Lead-silver slag: Zn 7.2%, Pb 5.3%, Cu 0.74%, In 125g / t, Ag 161g / t, Au 2.1g / t; Alumite slag: Zn 5.9%, Pb 3.6%, Cu 0.86% , In 72g / t, Ag 92g / t, Au 0.32g / t. Get respectively 200kg of above-mentioned blast furnace slag, 400kg of alumina slag, and 100kg of lead-silver slag (the mass ratio of alumina slag: lead-silver slag: blast furnace slag is 2:4:1), and the blast furnace slag, alumina slag and lead-silver slag that will take out The slag was mixed with a tank mixer for 10 minutes, and 70kg of water was added during the mixing process. It was detected that the water content of the mixture was 18%. The mixture was compacted with a hydraulic molding machine, and the agglomerate was dried at 200° C. for 12 hours to obtain 644 kg of dried agglomerate. Add 644kg dry agglomerate...
PUM
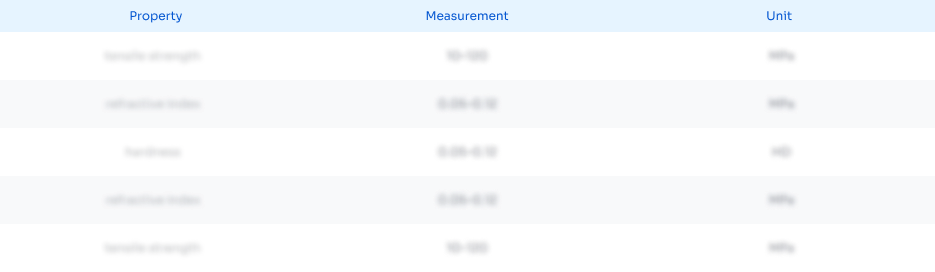
Abstract
Description
Claims
Application Information

- R&D
- Intellectual Property
- Life Sciences
- Materials
- Tech Scout
- Unparalleled Data Quality
- Higher Quality Content
- 60% Fewer Hallucinations
Browse by: Latest US Patents, China's latest patents, Technical Efficacy Thesaurus, Application Domain, Technology Topic, Popular Technical Reports.
© 2025 PatSnap. All rights reserved.Legal|Privacy policy|Modern Slavery Act Transparency Statement|Sitemap|About US| Contact US: help@patsnap.com