A high-efficiency automatic continuous production method for prepreg composite coils
A production method and prepreg technology, which is applied in the field of polymer composite material preparation, can solve the problems of large proportion of manual operation, difficulty, and complicated procedures, and achieve the effects of resisting external attacks, stable and uniform quality, and improving transverse strength
- Summary
- Abstract
- Description
- Claims
- Application Information
AI Technical Summary
Problems solved by technology
Method used
Image
Examples
Embodiment 1
[0040] The mono-oriented prepreg fabric roll is released from the longitudinal unwinding roll 1, with the side with fiber bundles facing up and the side with PE film facing down. The material is actively fed by a pair of pinch rollers 2, and the glue spraying device 3 evenly distributes the adhesive. Spray on the longitudinal cloth surface, pre-dry the glued prepreg cloth in the drying place 4, the drying temperature is 80°C, pass through the roller 5, and spread it on the composite platform 6, the composite platform 6 is fixed It is also equipped with heating and drying equipment with a temperature of 65°C to dry the unidirectional prepreg after gluing, and the longitudinal fabric is in a static state at this time. After the horizontal fabric is orthogonally compounded with it, continue to move forward vertically, the distance of the forward movement is the width of the horizontal fabric -0.7mm, stop and continue to compound the second piece of transverse material, the compoun...
Embodiment 2
[0043] The mono-oriented prepreg fabric roll is released from the longitudinal unwinding roll 1, with the side with fiber bundles facing up and the side with PE film facing down. The material is actively fed by a pair of pinch rollers 2, and the glue spraying device 3 evenly distributes the adhesive. Spray on the longitudinal cloth surface, the glued prepreg cloth is pre-dried in the drying place 4, the drying temperature is 90°C, passes through the roller 5, and spreads on the composite platform 6, which is fixed It is also equipped with heating and drying equipment with a temperature of 80°C to dry the unidirectional prepreg after gluing, and the longitudinal fabric is in a static state at this time. After the horizontal fabric is orthogonally compounded with it, continue to move forward in the longitudinal direction, and the forward distance is the width of the horizontal fabric -0.5mm. Stop and continue to compound the second piece of transverse material. The edge cutting ...
Embodiment 3
[0046] The mono-oriented prepreg fabric roll is released from the longitudinal unwinding roll 1, with the side with fiber bundles facing up and the side with PE film facing down. The material is actively fed by a pair of pinch rollers 2, and the glue spraying device 3 evenly distributes the adhesive. Spray on the longitudinal cloth surface, pre-dry the glued prepreg cloth in the drying place 4, the drying temperature is 100°C, pass through the roller 5, and spread it on the composite platform 6, the composite platform 6 is fixed It is also equipped with heating and drying equipment with a temperature of 95°C to dry the unidirectional prepreg after gluing, and the longitudinal fabric is in a static state at this time. After the horizontal fabric is orthogonally combined with it, continue to move forward in the vertical direction, and the forward distance is the width of the horizontal fabric -1mm, stop and continue to compound the second piece of transverse material, and the com...
PUM
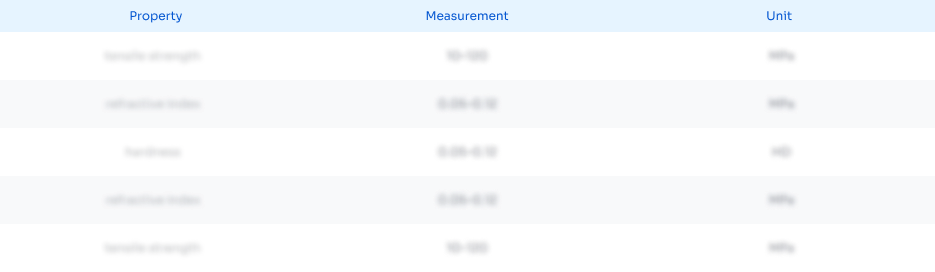
Abstract
Description
Claims
Application Information

- R&D
- Intellectual Property
- Life Sciences
- Materials
- Tech Scout
- Unparalleled Data Quality
- Higher Quality Content
- 60% Fewer Hallucinations
Browse by: Latest US Patents, China's latest patents, Technical Efficacy Thesaurus, Application Domain, Technology Topic, Popular Technical Reports.
© 2025 PatSnap. All rights reserved.Legal|Privacy policy|Modern Slavery Act Transparency Statement|Sitemap|About US| Contact US: help@patsnap.com