Manufacturing method of printing and dyeing wastewater filter material
A technology for filtering materials and printing and dyeing wastewater, applied in the fields of filtration and separation, separation methods, chemical instruments and methods, etc., can solve the problems of high cost, low moisture regain of chemical fibers, long time, etc., and achieve the effect of long service life
- Summary
- Abstract
- Description
- Claims
- Application Information
AI Technical Summary
Problems solved by technology
Method used
Image
Examples
Embodiment 1
[0017] A method for manufacturing a printing and dyeing wastewater filter material, comprising: using bast fiber yarn to make a fabric layer 1 with a spatial network structure, and performing low-temperature plasma treatment on it; Polyarylate fibers are used to make the filter material base layer 2, and the filter material base layer 2 is treated with low-temperature plasma, and the fabric layer 1 and the filter material base layer 2 are knitted together by a knitting process; the spinning solution is used for electrostatic spinning with a nanofiber electrospinning device. Spinning, so that the polymer solution forms a charged jet stream, and the charged polymer solution jet stream is stretched, thinned, bent, and split to be arranged on the surface of the filter material base layer 2 in a disordered manner to form a nanofiber membrane 3. Due to the high-speed impact of the polymer solution and its own adhesive properties, the nanofiber membrane 3 is bonded to the upper surfac...
Embodiment 2
[0019] A method for manufacturing a printing and dyeing wastewater filter material, comprising: using bast fiber yarn to make a fabric layer 1 with a spatial network structure and performing low-temperature plasma treatment on it; The arylate fiber is used to make the filter material base 2, and the filter material base 2 is treated with low-temperature plasma, and the fabric layer 1 and the filter material base 2 are knitted together by a knitting process; the spinning solution is used to conduct electrospinning with a nanofiber electrospinning device Wire, so that the polymer solution forms a charged jet stream, and the charged polymer solution jet stream is stretched, thinned, bent, and split to be arranged on the surface of the filter material base layer 2 in a disordered manner to form a nanofiber membrane 3 , due to the high-speed impact of the polymer solution and its own adhesive properties, the nanofiber membrane 3 is bonded to the upper surface of the filter material ...
Embodiment 3
[0021] A method for manufacturing a printing and dyeing wastewater filter material, comprising: using bast fiber yarn to make a fabric layer 1 with a spatial network structure and performing low-temperature plasma treatment on it; The arylate fiber is used to make the filter material base 2, and the filter material base 2 is treated with low-temperature plasma, and the fabric layer 1 and the filter material base 2 are knitted together by a knitting process; the spinning solution is used to conduct electrospinning with a nanofiber electrospinning device Wire, so that the polymer solution forms a charged jet stream, and the charged polymer solution jet stream is stretched, thinned, bent, and split to be arranged on the surface of the filter material base layer 2 in a disordered manner to form a nanofiber membrane 3 , due to the high-speed impact of the polymer solution and its own adhesive properties, the nanofiber membrane 3 is bonded to the upper surface of the filter material ...
PUM
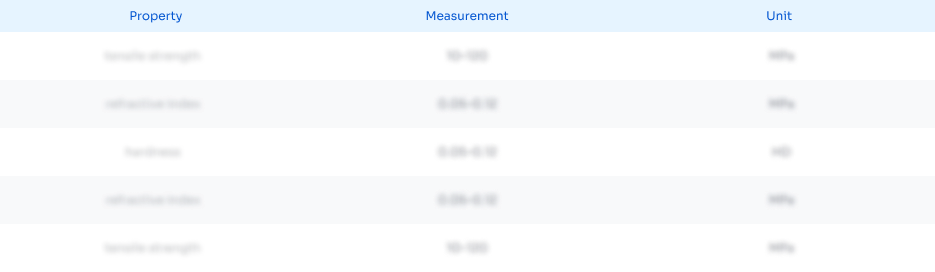
Abstract
Description
Claims
Application Information

- Generate Ideas
- Intellectual Property
- Life Sciences
- Materials
- Tech Scout
- Unparalleled Data Quality
- Higher Quality Content
- 60% Fewer Hallucinations
Browse by: Latest US Patents, China's latest patents, Technical Efficacy Thesaurus, Application Domain, Technology Topic, Popular Technical Reports.
© 2025 PatSnap. All rights reserved.Legal|Privacy policy|Modern Slavery Act Transparency Statement|Sitemap|About US| Contact US: help@patsnap.com