Spray-welding coating technology for hot-rolling laminar cooling roller and use fixture for technology
A laminar cooling and coating technology, applied in the direction of metal material coating process, coating, melting spray plating, etc., can solve the problems of affecting the remelting effect, affecting the life and quality of the spray welding roller table, etc.
- Summary
- Abstract
- Description
- Claims
- Application Information
AI Technical Summary
Problems solved by technology
Method used
Image
Examples
Embodiment Construction
[0018] A spray welding coating process for hot-rolled laminar flow cooling rolls, comprising the following steps:
[0019] 1) Roller blanking and processing before spraying:
[0020] 1.1) The seamless tube blank is used as the wool of the roller, and the wool is preprocessed to remove the oxide or fatigue layer on the surface, which has the effect of purifying, roughening or activating the surface;
[0021] 1.2) Texturize the roller, that is, turn the roller with a thread pitch of 0.5-1mm, an optimized pitch of 0.95mm, a depth of 0.5-1mm, and an optimized depth of 0.85mm;
[0022] 1.3) Degrease and decontaminate the rough-textured rollers;
[0023] 2) Preheat the workpiece: rotate the roller at a constant speed, and preheat the roller at the same time, the preheating temperature is 400-550°C;
[0024] 3) Spray welding coating: adjust the speed of the roller to 15-20 rpm, adjust the position of the spray gun and then turn on the spray gun, adjust the powder feeding amount and...
PUM
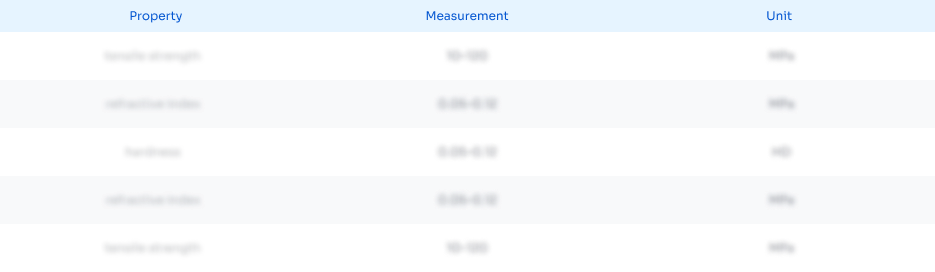
Abstract
Description
Claims
Application Information

- R&D
- Intellectual Property
- Life Sciences
- Materials
- Tech Scout
- Unparalleled Data Quality
- Higher Quality Content
- 60% Fewer Hallucinations
Browse by: Latest US Patents, China's latest patents, Technical Efficacy Thesaurus, Application Domain, Technology Topic, Popular Technical Reports.
© 2025 PatSnap. All rights reserved.Legal|Privacy policy|Modern Slavery Act Transparency Statement|Sitemap|About US| Contact US: help@patsnap.com